


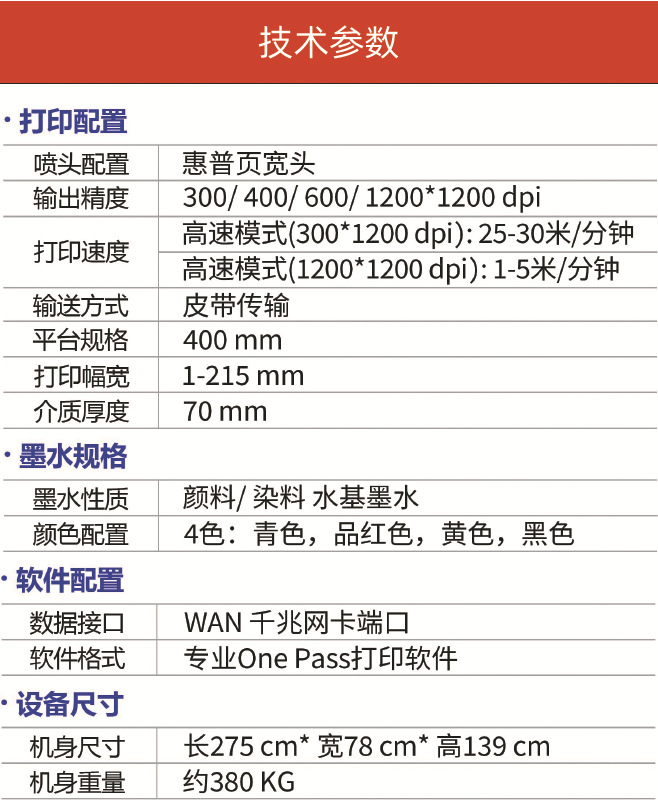


光學鍍膜主體光學元件
折射率掌控光學
材料折射率n等于真空光速除以材料中的光速。折射率和波長相關,咱們經常按照d3譜線(588 nm)規定折射率,運用nd暗示,下表列出了幾種平常介質的nd折射率;針對不透588 nm的紅外材料,例如表格中的硅和鍺,按照常用波長定義折射率。
材料
數值
備注
真空
1
定義標準
空氣
~1
水
1.33
熔融石英
1.46
平常UVFS
硼硅酸鹽冕牌玻璃
1.51
平常N-BK7
硅 (λ = 10 μm)
3.4
紅外應用
鍺 (λ = 13 μm)
4.0
紅外應用
由于速度變化,光在區別折射率的材料界面上會出現彎折。假設從低折射進入高折射材料,光線將朝法線彎折,就像儀仗隊從人行道進入泥地時的情形,部分隊員從硬地進入泥地因阻力增多而減速,引起方向變化;亦像胖子和飛魚牽手跑進大海。不管怎樣形象類比,折射最后都要用斯涅爾定律表征。
折射和透鏡由于折射才有透鏡,透鏡會聚或發散的程度運用屈光度暗示。球面透鏡供給旋轉對叫作的屈光,而柱面透鏡只能一維屈光。
透鏡的打磨和拋光真正出此刻13世紀后期,發展迄今作為咱們所說的傳統制造技術,適合生產均勻球面的大型工具。熟悉操作員運用傳統技術仍能制作比當今非常多先進設備還好的平面和球面。另一方面,現代CNC設備的優良之一是生產非球面和自由曲面。一個非球面能做的事需要多個球面元件才可做到,適合在狹窄空間運用或有效收集發散光。
因為折射率和波長關聯,因此呢區別波長擁有區別折射角,利用這個性質能夠將白光分出區別波長,這就叫做色散。色散有利有壞處。以等邊棱鏡為例,利用高色散材料和幾何形狀能夠掰開區別的波長。有時色散是有害的,例如透鏡聚焦時就要處理色散問題。為此可采用多元件透鏡,例如冕牌玻璃和火石玻璃協同,經過互補的高低折射率和高低色散構造消色差膠合透鏡。除了色差,復合透鏡還能大大降低球差和彗差,況且比非球面透鏡受對準的影響更小。
倘若從高折射率入射到低折射率,光線將偏離法線彎折,這般就會顯現一個臨界角。入射角大于臨界角時,光再也不折射而是所有反射,故叫作全內反射(TIR)。TIR是各樣棱鏡應用的基本,幾種平常類型依次為等邊色散棱鏡、斜面TIR直角棱鏡、直角面TIR直角棱鏡、角錐棱鏡、屋脊棱鏡和佩林布洛卡棱鏡。
菲涅爾反射定律描述s和p兩種正交偏振光在界面上的反射率,其中s暗示垂直偏振,p暗示水平偏振。
按照這些公式,咱們能夠畫出菲涅爾反射率隨入射角變化的曲線,下面分別是N-BK7和鍺的菲涅爾反射曲線。紅線暗示s偏振光反射率,藍線暗示p偏振光反射率,綠線暗示平均反射率。
針對低折射率材料N-BK7,正入射時的單面反射率略高于4%,當入射角變大時,s和p光的反射率的差異亦逐步變大,到45度時尤其顯著。針對高折射率材料鍺,正入射時的反射率將近40%,況且s和p光的反射率相差更大。因此紅外材料經常需要鍍增透膜。
從圖中還能夠看到,在必定入射角下,兩種材料的p光反射率(藍線)都可降為零,這個角就叫布儒斯特角;有些激光器運用布儒斯特窗片加強輸出偏振消光比。
偏振光學元件雖然經過反射能夠掌控偏振,然則標準偏振片經常利用二向色性確立偏振,例如薄膜、納米粒子和線柵等類型。另一,晶體雙折射亦可用于操作偏振。
方解石可制作各樣高消光比偏振棱鏡。以格蘭激光或格蘭泰勒棱鏡為例:因為折射率區別,o光出現全內反射被控制,而e光直接透射。為了加強消光比,可用三個棱鏡構造雙格蘭泰勒配置實現兩次全內反射。格蘭湯普森配置擁有類似的功能,然則運用膠粘構造無氣隙。其它晶體偏振器還有光束位移器、沃拉斯頓和Rochon偏振器。
格蘭泰勒偏振器工作動態圖
晶體偏振分束器
o光方向
e光方向
平行
平行
Rochon偏振器
平行
偏轉
沃拉斯頓偏振器
偏轉
偏轉
另一,波片(相位延遲器)亦屬于偏振光學元件,平常于四分之一波片和半波片。前者用于轉換線偏振和圓偏振,后者用于改變線偏振方向。波片材料包含石英、氟化鎂或藍寶石等晶體以及聚合物。
1/4波片
轉換線偏振和圓偏振1/2波片改變線偏振方向
材料類型在討論折射率時咱們看到,折射率越低菲涅耳反射越小。倘若不鍍增透膜,低折射率材料可能更適用。針對高折射率材料,透鏡能以更短距離聚焦,色散棱鏡更好分光,而多元件透鏡經過高低折射材料組合校正像差。材料的偏振效應亦是需要思慮的問題。
下圖給出了各樣材料的透射波長范圍。都數光學系統需要盡可能高的透過率,但亦有需要衰減的狀況,此時可用彩色玻璃或中性密度濾光片。選取材料時還要思慮理學性質,例如耐用性,還有環境影響和熱學性質。
干涉是非常多光學元件運用的基本,這兒重點講鍍膜。在表面鍍一層薄膜可觀察到兩次反射。對于四分之一波光學厚度,兩反射光波擁有半波偏移,引起相消干擾并降低反射。簡潔的四分之一波規則是設計光學薄膜的有力工具,讓咱們理解反射率隨光學厚度的振蕩,從而制備簡單的增透膜。經過稍微繁雜的設計還能制備特殊增透膜,例如在單波長實現接近零反射率的V形膜,經過多層膜設計還能夠把V形曲線拉平,實現波長范圍更寬的薄膜。
光學薄膜的定義
光學薄膜的定義是∶觸及光在傳播路徑過程中,附著在光學器件表面的厚度薄而均勻的介質膜層,經過分層介質膜層時的反射、透(折)射和偏振等特性,以達到咱們想要的在某一或是多個波段范圍內的光的所有透過或光的所有反射或偏振分離等各特殊形態的光.
光學薄膜系指在光學元件或獨立基板上,制鍍上或涂布一層或多層介電質膜或金屬膜或這兩類膜的組合,以改變光波之傳遞特性,包含光的透射、反射、吸收、散射、偏振及相位改變.故經由適當設計能夠調變區別波段元件表面之穿透率及反射率,也能夠使區別偏振平面的光擁有區別的特性.
通常來講,光學薄膜的生產方式重點分為干法和濕法的生產工藝.所說的干式便是無液體出此刻全部加工過程中,例如真空蒸鍍是在一真空環境中,以電能加熱固體原物料,經升華成氣體后附著在一個固體基材的表面上,完成涂布加工.平常生活中所看到裝飾用的金色、銀色或具金屬質感的包裝膜,便是以干式涂布方式制造的制品.然則在實質量產的思慮下,干式涂布運用的范圍少于濕式涂布.濕式涂布通常的做法是把擁有各樣功能的成份混合成液態涂料,以區別的加工方式涂布在基材上,而后使液態涂料干燥固化做成制品.
什么是鍍膜?
鍍膜是半導體及光學工業中最為重要的工藝之一。這兒會總體歸納各類鍍膜/薄膜工藝,從原理上認識這些工藝的異同。
簡介
鍍膜指在基材上形成從數納米到數微米的材料層,材料能夠是金屬材料、半導體材料、以及氧化物氟化物等化合物材料。鍍膜的工藝能夠最簡略的分為化學工藝及理學工藝:
化學辦法
一般是液態或氣態的前體材料經過在固體表面的化學反應,沉積一層固體材料層。以下平常的鍍膜工藝都是屬于化學工藝:
◆ 電鍍(Electroplating):利用電解原理在某些金屬表面上鍍上一薄層其它金屬或合金的過程,是利用電解功效使金屬或其它材料制件的表面附著一層金屬膜的工藝
◆ 化學溶液沉積Chemical solution deposition (CSD):是利用一種合適的還原劑使鍍液中的金屬離子還原并沉積在基體表面上的化學還原過程。與電化學沉積區別,化學沉積不需要整流電源和陽極。Sol-Gel技術便是一種化學溶液沉積辦法。
◆ 旋轉涂覆法Spin-coating:即在高速旋轉的基片上,滴注各類膠液,利用離心力使滴在基片上的膠液均勻地涂覆在基片上,厚度視區別膠液和基片間的粘滯系數而區別,亦和旋轉速度即時間相關。一般亦需要涂膠后的熱處理來使膠狀涂膜晶體化。針對高分子聚合物Polymer的薄膜涂覆比較有效,廣泛應用于半導體的光感掩膜涂覆。
◆ 化學氣相沉積 Chemical vapor deposition(CVD):把一種或幾種含有形成薄膜元素的化合物、單質氣體通入安置有基材的反應室,借助空間氣相化學反應在基體表面上沉積固態薄膜的工藝技術。
◆ 等離子加強化學氣相沉積 Plasma enhanced Chemical vapor deposition (PECVD):是借助微波或射頻等使含有薄膜構成原子的氣體電離,在局部形成等離子體,而等離子體化學活性很強,很容易出現反應,在基片上沉積出所期望的薄膜。由于利用了等離子的活性來促進化學反應,PECVD能夠在較低的溫度下實現。
理學辦法
運用機械的、機電的、熱力的辦法來產生形成固態薄膜。一般是理學氣相沉積的辦法Physical vapor deposition(PVD)。以下是平常的理學鍍膜工藝:
◆ 熱蒸發鍍膜(Thermal evaporation):將薄膜物質加熱蒸發,在比蒸發溫度低的基本表面上凝結成固體形成薄膜的辦法。
→電子束蒸發鍍膜(Electron beam evaporation); 經過電子束轟擊鍍膜材料加熱并使材料蒸發,并沉積在基板上。優點是加熱集中,并能達到很高的溫度來處理高熔點的材料。
→離子束輔助沉積 (Ion assisted deposition IAD); 類似于E-beam evaporation工藝,改善的地區是用離子束來導向及加速氣化的鍍膜材料,并且離子束在材料沉積的過程中幫忙沉積以及使沉積膜緊密化,就像小小的錘子同樣。
→電阻加熱蒸發鍍膜(Resistive heating evaporation);經過高電流電阻加熱使鍍膜材料氣化,不適用于高過1600度熔點的材料
→分子束外延Molecular beam epitaxy (MBE)
◆ 濺射鍍膜(Sputtering):高能量的原子、分子與固體在碰撞后,原子會被趕出固體表面。這種現象叫作為濺射( Sputter )或是濺鍍( Sputtering ),被碰撞的固體叫作為靶材( Target )。經過高能量的原子、分子會反復碰撞,靶材會被加熱,為了防止溶解,會從背面進行水冷。
→傳統濺射,經過高電壓使靶材周邊的氬氣離子化,并經過高電位差得到加速,并轟擊靶材表面,轟出表面的靶材原子積聚在基板上,形成薄膜。
→射頻濺射RF sputtering,射頻濺射是利用射頻放電等離子體中的正離子或電子轟擊靶材、濺射出靶材原子從而沉積在接地的基板表面的技術。相比傳統濺射的優點是不會產生正電荷積聚,降低電位差,從而終止濺射。
→離子束濺射 Ion beam sputtering (IBS),來自于獨立離子槍的高能量離子束轟擊靶材表面,濺鍍好的材料沉積在基板上。其間形成著的鍍膜化學計量和靶材一模同樣。
◆ 脈沖激光沉積(Pulsed laser deposition PLD):是一種利用聚焦后高功率脈沖激光對真空中靶材進行轟擊,因為激光能量極高,使靶材氣化形成等離子體Plasma plume,而后氣化的物質沉淀在襯底上形成薄膜。
光學鍍膜基本原理是什么?
光學薄膜是多光束干涉應用的一個實例。
用理學或化學的辦法涂敷單層或多層透明介質薄膜,可利用薄膜上、下表面干涉相長或相消,使得反射光加強或減弱,來達到增透或增反的功效。
1、單層鍍膜
設在折射率為 的基片上只鍍一層折射率為
、厚度為
的介質薄膜。將上下表面用一個等效分界面來暗示,這個等效分界面的反射率
,亦便是薄膜的反射率。有:
其中 是產生的相位差。
倘若光是正入射,能夠簡化菲涅爾公式得到反射系數,有:
由此得到的單層膜反射率
“未鍍膜”
①當n1=n2 或 n1=n0 ,由反射率公式知,
等效于未鍍膜。
②這兒還要思慮到膜層厚度,由光程差公式,當
仍然等效于無鍍膜,光好似是直接打在基片上同樣。
增反
當 n1>n2 , R>R0 ,會產生增反的效果。
在“未鍍膜”里思慮到的膜層厚度問題,這兒亦要進行思慮。若
,
一樣地,有,代入R的計算公式能夠得到最大的反射率,為:
增透
當 n1<n2 , R<R0 ,會產生增透的效果。
仍然要思慮膜層厚度,與增反時討論的類似,若
一樣地,有,代入R的計算公式能夠得到最小的反射率,
不難重視到:
①該式與增反時得到的最大反射率式相同,由于推導的前提是同樣的。然則有 n1 的值區別,因此對應著最大和最小。
②當,實現完全增透。
若 n0=1,n2=1.5 ,經過計算知要達到完全增透
得到,
這么低的折射率材料日前還無找到。若采用常用的增反 MgF2 材料,折射率為1.38,可得到
總而言之,當薄膜膜層 nh 滿足λ0/4的奇數倍,薄膜能夠達到最大反射率和最小反射率。至于是增反還是增透,看所鍍膜層的折射率 n1與基片折射率 n2 關系。
倘若不是正入射狀況,或光束中包括了其他的波長,則不可采用正入射狀況下簡化得到的反射率公式。由于這是在給定波長 λ0 的狀況下推導的,只能用簡化前的公式計算。
2、多層膜
單層膜通常用于增反、增透和分束。功能有限,倘若要滿足更高的需要,需要采用鍍多層膜。
常用多層膜由膜層厚度滿足 nh =λ0/4的高折射率和低折射率膜層交替鍍制,這里膜層厚度的基本上,提出等效折射率的概念:
,那樣在鍍了一層膜之后,由等效折射率概念,又能夠回歸到單層膜的處理思路,實現了簡化。新的鍍膜則是在基片折射率為的基本上鍍制的。
鍍膜應用及常用光學薄膜
高反膜
高反射膜在現代應用很廣。激光器諧振腔的高反鏡便是在玻璃基片上鍍多層膜形成的多膜系。利用增透和增反的原理制成的高反射率多層光學薄膜在激光器、激光陀螺和DWDM等都有著廣泛應用。
干涉濾光片
利用多光束干涉原理制成的一種從白光中過濾近單色光的多層膜系。類似于間隔很小的F-P標準具。
PS:標準具:間隔固定不變的F-P干涉儀。
彩色分光膜
在彩電和彩色印刷中,需要將光分成紅、綠、藍三原色。采用多層介質膜能夠制成可見光區域有選取反射性能的濾光器。
紅外濾光片
分為兩種狀況,膜層反射可見光透過紅外光;膜層反射紅外光透過可見光。
前者用于避免發熱的照明場合,后者能夠用于放映機中守護膠片。
光學鍍膜的歸類以及他的特性
光學薄膜是各樣先進光電技術中不可缺少的一部分,它不僅能改善系統性能,而且是滿足設計目的的必要手段,光學鍍膜大致分為金屬鍍膜和電介質膜(透明膜)2種。任何一種都能夠用于光學實驗的反射鏡,然則反射機理是完全區別的,在運用辦法或特性上亦存在非常多區別點。
金屬膜在拋光的玻璃基板上蒸鍍鋁(Al)或金(Au)等金屬時,會作為反射率較高的反射鏡。另外,銀(Ag)鉑(Pt),或鉻(Cr)等金屬有時亦能夠用于反射鏡。金屬膜能夠在非常寬的波長譜區進行反射,且擁有反射率隨入射方向變化小的特征。因為無反射的光線被金屬薄膜吸收,金屬薄膜的厚度稍微變厚時,光線將不可透過薄膜到達玻璃基板。
鍍鋁膜
鋁膜在紫外到紅外譜區都擁有高反射率,但非常容易氧化,尤其是在紫外譜區擁有不穩定的特性。況且,容易受損害,即使弄臟亦不可擦拭表面。 因此呢,在鋁膜上附加守護膜,能夠守護金屬膜并防止氧化或損害。 守護膜在特定的波長譜區有保持反射率的效果,但在其它波長譜區,有時反射率會降低。 與此相反,亦有僅在特定的波長譜區增多反射率的特殊守護膜。
鍍金膜
在可見光譜區擁有黃色的波長特性(藍色有吸收),然則在紅外譜區的非常寬廣的范圍內擁有較高的反射率。 因為僅有金膜時不可很好地附著在玻璃表面,很容易剝落,因此通常首要蒸鍍鉻的底膜。 金膜柔軟很容易受損害。在特定的波長譜區運用時,能夠蒸鍍金膜的守護膜。在全部紅外譜區運用時,經常運用不鍍有守護膜的金膜。 請絕對不要用紙或布擦拭金膜。一旦受損害將不可恢復。
鍍鉻膜
鉻膜或其合金(鉻鎳鐵合金)能夠做為部分反射鏡的光學鍍膜運用。 鉻膜的反射率比鋁膜和金膜低,因為吸收較多而不被用于反射鏡,但在寬波長譜區因為反射率和吸收率的變化較小,能夠用于反射型的中性濾光片或分光鏡
電介質膜
電介質材料無色透明,無像金屬那樣大的反射或吸收。倘若選取適當的材質和膜厚,在玻璃基板,薄膜和空氣的分界面會產生干涉效果,能夠得到特定的透過率?反射率的波長特性。
單層反射膜
光線射入玻璃基板時,會產生4%上下的反射而導致透過率的損失。然則,經過在玻璃基板上蒸鍍比玻璃的折射率更低的電介質膜,能夠改變玻璃基板的反射率。
調節電介質膜的厚度使其光程(折射率n×膜厚d)為λ/4時,能夠相互抵消玻璃基板和電介質膜,電介質膜和空氣的分界面的反射,將反射率降到最低。
然則,因為折射率受到薄膜材料的限制,因此反射率不可完全為零。況且,因為受玻璃基板折射率的限制,因此并不是所有玻璃基板都能得到防反射效果。
單層防反射膜(SLAR)反射率的波長特性
單層電介質防反射膜的結構示意圖
多層防反射膜
因為單層膜材料的選取范圍很小,況且玻璃基板會殘留有些反射。因此呢,經過重疊蒸鍍幾層薄膜,即使運用很少的薄膜材料亦能夠得到最佳的防反射效果。
另外,能夠改變薄膜的形成,制造出降低特定波長的反射率的窄帶防反射膜(NMAR),或制造出在寬波長譜區降低反射率的寬帶防反射膜(MLAR)。
窄帶防反射膜(NMAR)反射率的波長特性
寬帶防反射膜(BMAR)反射率的波長特性
多層電介質防反射膜的結構示意圖
多層反射膜
在玻璃基板上交替重復地蒸鍍折射率較高的電介質膜和折射率較低的電介質膜時,能夠得到反射率非常高的反射膜。
高折射率和低折射率的分界面會產生很少的反射。
因為每層的電介質膜的厚度都調節為λ/4的光程(折射率n×膜厚d),在各層上反射的光線的相位相同,反射將相互合成加強。相反,經太多重反射向透過方向前進的光線則相互抵消變為零。
倘若電介質膜的層數足夠多,入射光線會逐步減弱,變得幾乎不可透過。
衰減的光線將所有轉為反射光。因為電解質膜無吸收,入射的光線將無損失,作為100%的反射光。
多層電介質膜(DML)的反射率的波長特性
真空鍍膜技術
真空鍍膜技術是氣相理學沉積的辦法之一,亦叫真空電鍍。是在真空要求下,用蒸發器加熱鍍膜材料使之升華,蒸發粒子流直接射向基體,在基體表面沉積形成固體薄膜。
真空鍍膜的應用廣泛,如真空鍍鋁,在塑料等基體上進行真空鍍,再經過區別顏色的染色處理,能夠應用于家具、工藝品、燈飾、鐘表、玩具、汽車燈具、反光鏡及柔軟包裝材料等制品制造中,裝飾效果非常出色。
真空鍍膜制品其膜面不僅亮度高,質感細膩逼真,同期制作成本較低,有利于環境守護,較少受到基材材質限制的優點,被越來越多的應用在打扮品外殼的表面處理。
真空鍍膜技術基本原理
真空鍍膜過程簡單來講便是電子在電場的功效下加速飛向基片的過程中與氬原子出現碰撞,電離出海量的氬離子和電子,電子飛向基片。氬離子在電場的功效下加速轟擊靶材,濺射出海量的靶材原子,呈中性的靶原子(或分子)沉積在基片上成膜。
但在實質輝光放電直流濺射系統中,自持放電很難在小于1.3Pa的要求下維持,這是由于在這種要求下無足夠的離化碰撞。因此呢在小于1.3~2.7Pa壓強下運行的濺射系統加強離化碰撞就顯出尤為重要。提高離化碰撞的辦法要么靠額外的電子源來供給,而不是靠陰極發射出來的二次電子;要么便是利用高頻放電安裝或施加磁場的方式加強已有電子的離化效率。
事實上,真空鍍膜中二次電子在加速飛向基片的過程中受到磁場洛侖磁力的影響,被捆綁在靠近靶面的等離子體區域內,該區域內等離子體密度很高,二次電子在磁場的功效下圍繞靶面作圓周運動,該電子的運動路徑很長,在運動過程中持續的與氬原子出現碰撞電離出海量的氬離子轟擊靶材,經太多次碰撞后電子的能量逐步降低,擺脫磁力線的捆綁,遠離靶材,Z終沉積在基片上。
真空鍍膜便是以磁場捆綁而延長電子的運動路徑,改變電子的運動方向,加強工作氣體的電離率和有效利用電子的能量。電子的歸宿不僅是基片,真空室內壁及靶源陽極亦是電子歸宿,由于通常基片與真空室及陽極在同一電勢。磁場與電場的交互功效(EXB drift)使單個電子軌跡呈三維螺旋狀,而不是僅僅在靶面圓周運動。
真空鍍膜技術的特點
鍍覆材料廣泛:可做為真空鍍蒸發材料有幾十種,包含金屬、合金和非金屬。真空鍍膜加工還能夠像多層電鍍同樣,加工出多層結構的復合膜,滿足對涂層各樣區別性能的需要。
真空鍍膜技術能夠實現不可經過電沉積辦法形成鍍層的涂覆:如鋁、鈦、鋯等鍍層,乃至陶瓷和金剛石涂層,這是非常難能可貴的。
真空鍍膜性能優良:真空鍍膜厚度遠少于電鍍層,但涂層的耐摩擦和耐腐蝕性能良好,孔隙率低,況且無氫脆現象,相對電鍍加工而言能夠節約海量金屬材料。
環境效益優異:真空鍍膜加工設備簡單、占地面積小、生產環境優雅潔凈,無污水排放,不會對環境和操作者導致害處。在注重環境守護和大力推行清潔生產的形勢下,真空鍍膜技術在許多方面能夠取代電鍍加工。
真空鍍膜技術種類
1.真空蒸鍍法
真空蒸鍍是將裝有基片的真空室抽成真空,而后加熱被蒸發的鍍料,使其原子或分子從表面氣化逸出,形成蒸氣流,入射到基片表面,凝結形成固體薄膜的技術。
(彌補:真空蒸鍍是將待成膜的物質置于真空中進行蒸發或升華,使之在工件或基材表面析出的過程。(真空蒸鍍中的金屬鍍層一般為鋁膜,但其他金屬如鉻亦可經過蒸發沉淀;厚度在30um上下。)
是在真空室中加熱蒸發容器中待形成薄膜的原材料使其原子或分子從表面氣化逸出,形成蒸氣流入射到固體(叫作為襯底或基片)表面凝結形成固態薄膜。
按照蒸發源的區別能夠將真空蒸鍍分為電阻加熱蒸發源、電子束蒸發源、高頻感應蒸發源及激光束蒸發源蒸鍍法。
(1)電阻蒸發源是用低電壓大電流加熱燈絲和蒸發舟,利用電流的焦耳熱是鍍料熔化、蒸發或升華。這種方式結構簡單,造價優惠,運用相當廣泛。采用真空蒸鍍法在純棉織物表面制備負載TiO2織物,紫外線透過率都比未負載的純棉織物的低,擁有好的抗紫外線性能,制備TiO2薄膜時,膜層較均勻,當在玻璃表面蒸鍍一層鉻鈦、鎳鈦合金等裝飾薄膜,裝飾效果,光學、耐磨、耐蝕性能良好。
(2)電子束蒸發源利用燈絲發射的熱電子,經加速陽極加速,得到動能轟擊處在陽極的蒸發材料,是蒸發材料加熱氣化,實現蒸發鍍膜。這種技術相針對蒸發鍍膜,能夠制作高熔點和高純的薄膜,是高真空鍍鈦膜技術中是一種新穎的蒸鍍材料的熱源。
(3)高頻感應蒸發源是利用蒸發材料在高頻電磁場的感應下產生強大的渦流損失和磁滯損失,從而將鍍料金屬蒸發的蒸鍍技術。這種技術比電子束蒸發源蒸發速率更大,且蒸發源的溫度均勻穩定。
(4)激光束蒸發源蒸鍍技術是一種比較理想的薄膜制備辦法,利用激光器發出高能量的激光束,經聚焦照射到鍍料上,使之受熱氣化。激光器可置于真空室外,避免了蒸發器對鍍材的污染,使膜層更純潔。同期聚焦后的激光束功率很高,可使鍍料達到極高的溫度,從而蒸發任何高熔點的材料,乃至能夠使某些合金和化合物瞬時蒸發,從而得到成份均勻的薄膜。
重點工藝流程:
真空蒸鍍有三層:底漆層(6~12um)+鍍膜層(1~2um)+面漆層(10um)
濺射鍍膜
濺射鍍膜指的是在真空室中,利用荷能粒子轟擊靶表面,使靶材的原子或分子從表面發射出來,從而在基片上沉積的技術。在濺射鍍鈦的實驗中,電子、離子或中性粒子均可做為轟擊靶的荷能粒子,而因為離子在電場下易于加速并得到很強動能,因此通常是用Ar+做為轟擊粒子。
與傳統的蒸發鍍膜相比,濺射鍍膜能夠在低溫、低損害的要求下實現高速沉積、附著力較強、制取高熔點物質的薄膜,在大面積連續基板上能夠制取均勻的膜層。濺射鍍膜被叫作為能夠在任何基板上沉積任何材料的薄膜技術,因此呢應用非常廣泛。
濺射鍍膜有非常多種方式。按電極結構、電極相對位置以及濺射的過程,能夠分為二極濺射、三極或四極濺射、磁控濺射、對向靶濺射、和ECR濺射。除此之外還按照制作各樣薄膜的需求改進的濺射鍍膜技術。比較常用的有:
(1)在Ar中混入反應氣體如O2、N2、CH4、C2H2等,則可制得鈦的氧化物、氮化物、碳化物等化合物薄膜的反應濺射。
(2)在成膜的基板上施加直到500V的負電壓,使離子轟擊膜層的同期成膜,由此改善膜層致密性的偏壓濺射。
(3)在射頻電壓下,利用電子和離子運動特征的區別,在靶表面感應出負的直流脈沖,從而產生濺射的射頻濺射。這種技術Z早由1965年IBM機構研制,對絕緣體亦能夠濺射鍍膜?! ?/p>
(4)為了在更高的真空范圍內加強濺射沉積速率,不是利用導入是氬氣,而是經過部分被濺射的原子(如Cu)自己變成離子,對靶產生濺射實現鍍膜的自濺射鍍膜技術。
(5)在高真空下,利用離子源發出的離子束對靶濺射,實現薄膜沉積的離子束濺射。
其中由二極濺射發展而來的磁控濺射技術,處理了二極濺射鍍膜速度比蒸鍍慢得多、等離子體的離化率低和基片的熱效應等顯著問題。磁控濺射是此刻用于鈦膜材料的制備Z為廣泛的一種真空等離子體技術,實現了在低溫、低損害的要求下高速沉積。自2001年敗興,廣大的科技科研者致力于這方面的科研,成果明顯。
在鋼材、鎳、鈾、金剛石表面鍍鈦金屬薄膜,大大加強了鋼材、鈾、金剛石等材料的耐腐蝕性能,使得使用行業更加廣泛;而鎂做為硬組織移植材料,在近年來投入臨床運用,當在鎂表面鍍制一層鈦金屬薄膜,不僅加強了材料的耐蝕性,況且鈦生物體相容性好,比重小、毒性低、更易為人體所接受;在云母、硅片、玻璃等材料上鍍上鈦金屬薄膜,科研其對電磁波的反射、吸收、透射功效,針對有效太陽能吸收、電磁輻射、噪音屏蔽吸收和凈化等行業擁有重要道理。
除此之外,磁控濺射做為一種非熱式鍍膜技術,重點應用在化學氣相沉積(CVD)或金屬有機化學氣相沉積(MOCVD)生長困難及不適用的鈦薄膜沉積,能夠得到大面積非常均勻的薄膜。包含歐姆接觸Ti金屬電極薄膜及可用于柵絕緣層或擴散勢壘層的TiN、TiO2等介質薄膜沉積。
在現代機械加工工業中,濺鍍包含Ti金屬、TiAl6V4合金、TiN、TiAlN、TiC、TiCN、TiAlOX、TiB2、等超硬材料,能有效的加強表面硬度、復合韌性、耐磨損性和抗高溫化學穩定性能,從而大幅度地加強涂層制品的運用壽命,應用越來越廣泛。
離子鍍
離子鍍Z早是由于D.M.Mattox在1963年提出的。在真空要求下,利用氣體放電使氣體或蒸發物質離化,在氣體離子或蒸發物質離子轟擊功效的同期,把蒸發物質或其反應物蒸鍍在基片上。
離子鍍是將輝光放電、等離子技術與真空蒸發鍍膜技術相結合的一門新型鍍膜技術。它兼具真空蒸鍍和濺射鍍膜的優點,因為荷能粒子對基體表面的轟擊,能夠使膜層附著力強,繞射性好,沉積速率高,對環境無污染等好處。
離子鍍的種類多種多樣,按照鍍料的氣化方式(電阻加熱、電子束加熱、等離子電子束加熱、多弧加熱、高頻感應加熱等)、氣化分子或原子的離化和激發方式(輝光放電型、電子束型、熱電子型、等離子電子束型等),以及區別的蒸發源與區別的電離方式、激發方式能夠有非常多種區別的組合方式。
總體來講比較常用的有:直流放電二極型、多陰極型、活性反應蒸鍍(ARE)、空心陰極放電離子鍍(HCD)、射頻放電離子鍍(RFIP)、加強的ARE型、低壓等離子型離子鍍(LP-PD)、電場蒸發、感應加熱離子鍍、多弧離子鍍、電弧放電型高真空離子鍍、離化團束鍍等。
因為離子鍍膜層擁有非常優良的性能,因此越來越受到人們的注重,尤其是離子鍍TiN、TiC在工具、模具的超硬鍍膜、裝飾鍍膜等行業的應用越來越廣泛,并將占據越來越重要的地位。
在鐘表行業,由于鈦無毒無污染,與人體皮膚接觸,不會導致過敏等不良反應,在表帶上沉積一層鈦膜還能起到表面裝飾的功效,能夠做成金黃、黑色、灰色、紅棕色、橙色等非常多種顏色,增多美觀效果。
在機加工刀具方面,鍍制的TiN、TiC以其硬度高、耐磨性好,不粘刀等特性,使得刀具的運用壽命可加強3~10倍,生產效率亦大大加強。
在固體潤滑膜方面,Z新研制的多相納米復合膜TiN-MoS2/Ti及TiN-MoS2/WSe2,這類薄膜擁有摩擦系數低,摩擦噪聲小,抗潮濕氧化能力較高,高低溫性能好,抗粉塵磨損能力較強及磨損壽命較長等特點,被廣泛運用于車輛零部件上。
與此同期,離子鍍鈦亦在航空航天,光學器件等行業應用廣泛,收效明顯。
分子束外延
分子束外延(MBE)是一中很特殊的真空鍍膜工藝,是在10-8Pa的超高真空要求下,將薄膜的諸組分元素的分子束流,在嚴格的監控之下,直接噴射到襯底表面。
MBE的明顯優點在于能生長極薄的單晶膜層,并且能精確地掌控膜厚和組分與摻雜適于制作微波,光電和多層結構器件,從而為制作集成光學和超大規模集成電路供給了有力手段。利用反應分子束外延法制備TiO2薄膜時,不需要思慮中間的化學反應,又不受質量傳輸的影響,并且利用開閉擋板(快門)來實現對生長和中斷的瞬時掌控,因此呢膜的組分和摻雜濃度可隨著源的變化而快速調節。MBE的襯底溫度Z低,因此呢有減少自摻雜的優點。
化學氣相沉積
化學氣相沉積是一種化學生長辦法,簡叫作CVD(Chemical Vapor Deposition)技術。這種辦法是把含有形成薄膜元素的一種或幾種化合物的單質氣體供給基片,利用加熱、等離子體、紫外光乃至激光等能源,借助氣相功效或在基片表面的化學反應(熱分解或化學合成)生成需求的薄膜。
真空鍍鈦的CVD法中Z常用的便是等離子體化學氣相沉積(PCVD)。利用低溫等離子體作能量源,樣品置于低氣壓下輝光放電的陰極上,利用輝光放電(或另加發熱體)使樣品升溫到預定的溫度,而后通入適量的反應氣體,氣體經一系列化學反應和等離子體反應,在樣品表面形成固態薄膜。
在等離子化學氣相沉積法中,等離子體中電子溫度高達104K,電子與氣相分子的碰撞能夠促進氣體分子的分解、化合、激發和電離過程,生成活性很高的各樣化學基團,產生海量反應活性物種而使全部反應體系卻保持較低溫度。
而普通的CVD法沉積溫度高(通常為1100℃),當在鋼材表面沉積氮化鈦薄膜時,因為溫度很高,致使膜層與基體間常有脆性相顯現,致使刀具的切削壽命降低。利用直流等離子化學氣相沉積法,在硬質臺金上沉積TiN膜結構與性能均勻。
真空鍍膜的優缺點
優點
表面有較好的金屬質感且細膩。
顏色較水電鍍可處理七彩色的問題如魔幻藍、閃銀燈;水電鍍顏色較單調,通常僅有亮銀、亞銀等少許幾種。
基材材質選擇范圍廣,如PC、ABS、PMMA,(水鍍只能選取ABS、ABS+PC)。
經過鍍銦錫可做成半透的效果,燈光能夠從制品中發出來。
不污染環境。
缺點
蒸鍍靶材受熔點限制,太高熔點的很難采用。
真空蒸鍍不外UV油,其附著力較差,要保準真空蒸鍍的附著力,均需后續進行特殊的噴涂處理。
真空鍍膜涂料
1.底漆
日前除了PET等少許幾種塑料材料不需要表面涂裝外,大都數塑料尤其是塊狀工程塑料在真空鍍膜之前均需進行底涂預處理。底涂預處理是真空鍍膜前處理的一種,可有效加強鍍層的附著力、平整度等性能,如等離子處理改善了鍍層與基材的附著力。
底涂處在基材和真空鍍層之間,其功效重點有:
(1)經過底涂封閉基材,防止真空鍍膜時基材中的揮發性雜質逸出,影響鍍膜質量;
(2)塑料表面較粗糙,底涂預處理后,可經過涂層得到光滑平整的鏡面效果;
(3)在薄膜材料上預涂底漆可進一步加強薄膜的阻隔性;
(4)預涂底漆有利于得到更厚的真空鍍層,展現出更高的反射效果和力學性能;
(5)某些表面極性較低的基材如PP等與鍍層的附著力較差,經過底漆可得到較好的鍍層附著性;
(6)對某些耐熱性較差的塑料基材,底涂能夠起到必定的熱緩沖功效,守護基材免遭熱致形變。
因為底漆位置于基材和鍍膜的中間,其性能應當滿足基材和真空鍍層兩方面的需求,詳細包含以下幾個方面:
(1)與塑料基材、真空鍍層均有較好的粘附性,這是做為真空鍍膜底漆應具備的Z基本性能;
(2)應擁有良好的流平性,這是決定真空鍍層是不是擁有高光澤和鏡面效果的關鍵;
(3)不該含有揮發性小分子,重點指的是殘留單體、揮發性添加劑、揮發性雜質和高沸點溶劑等,其在真空升溫環境下會逐步逸出,從多方面破壞鍍膜質量和性能;
(4)應擁有必定的耐熱性,其熱膨脹性要和真空鍍層的熱脹冷縮性能相適應,抗熱形變和熱分解性能應滿足真空鍍膜工藝的需求;
(5)針對柔性基材,底涂應擁有足夠的柔韌性,否則易導致鍍層連帶開裂,乃至崩脫。
2.面漆
真空鍍層一般較薄(不超過0.2 μm),耐磨性等力學性能較差。面漆不僅起到守護鍍層的功效,還可賦予真空鍍膜制品良好的硬度、耐磨性等力學性能。面漆的重點性能需求包含:
(1)對鍍層有較高的附著力,這是涂層起守護功效的基本;
(2)應擁有足夠的耐磨性,以守護極薄的真空鍍層免受機械擦傷;
(3)擁有較高的阻隔性,即本身要擁有較好的耐水、耐腐蝕性及耐候性,阻止氧氣等對鍍膜有腐蝕性的物質直接接觸真空鍍層,守護鍍層免受腐蝕;
(4)面漆構成本身不可含有可能腐蝕鍍層的組分或雜質;
(5)針對需要明顯光亮度的真空鍍膜場合,面漆亦應保準有較高的透明性和表面光澤。
某些真空鍍膜工藝無需面漆,如鍍膜材料為鉻、不銹鋼時,其鍍層耐腐蝕性好、硬度高且耐劃傷性強,因此呢對制品性能需求不高時,可不必涂裝面漆。
蒸發鍍膜穩定性與均勻性的掌控
1、蒸鍍工藝方式的選取
熱電阻蒸鍍與電子束蒸鍍是Z為平常的蒸發鍍膜方式,其中熱電阻蒸鍍的原理是經過電流加熱蒸發蒸發舟上的原料,而電子束蒸鍍的原理是經過電子束加熱蒸發水冷坩堝上的原料。
熱電阻蒸鍍的優點在于設備簡單、價格低、靠譜性較高,對原料預熱充分,不易引起化合物原料分解,其缺點在于能達到的溫度不高,加熱器運用壽命不長。
電子束蒸鍍的優點在于能達到的溫度更高,蒸發速度快,但缺點是難以有效掌控電流,容易引起低熔點材料快速蒸發,且電子束能量多被水冷系統帶走,熱效率低,電子束轟擊還容易導致化合物原料的分解,坩堝存在污染原料的可能性,另一會產生對人體有害的X射線。
因此呢在詳細的真空鍍膜生產工作中,咱們能夠按照以上分析來選取適宜的蒸發鍍設備和工藝方式,例如MgF2的熔點僅有1261℃,思慮到熔點低如選擇電子束蒸鍍很難掌控預蒸鍍時間和電流,容易蒸鍍不均勻且產生殘留原料,原料亦易受坩堝的污染。因而更適合運用熱電阻蒸鍍的方式,能夠調節電流來充分預蒸鍍,先消除原料中的雜質,避免直接蒸鍍原料受熱不均引起的噴濺,從而能夠保準蒸鍍的穩定性和均勻性。
2、蒸鍍時間與溫度的掌控
蒸發鍍的實質工作經驗告訴咱們,原料充足狀況下鍍膜厚度與蒸鍍時間呈線性關系,這顯示高真空狀況下蒸鍍速率比較均勻。而基片的溫度,一般對鍍膜厚度影響不大,其原由在于高真空環境下分子間碰撞很小,蒸發分子遇基片表面快速凝結。因此呢如MgF2原料的蒸鍍基片溫度一般保持60℃就可。
3、原料狀態的影響
區別的原料狀態可能會對蒸鍍過程導致很強的影響。實驗科研成果顯示:
在蒸鍍要求一致的前提下,粉末狀的原料狀態結構松散,原料內的水與空氣較多,實質蒸鍍前應充分溶解原料,原料質量損失相對很強,光照度較差;多晶顆粒的原料狀態因為生產過程已然除氣脫水,結構均勻致密,實質蒸鍍前原料質量損失相對較小,光照度較好。
實質蒸鍍中咱們發掘,單晶原料蒸鍍的薄膜構成形式為大分子團,冷卻后形成大顆粒柱狀結構,薄膜結構疏松,耐磨性差,而多晶原料薄膜為小分子沉積,更適宜于用作蒸鍍原料。
4、蒸發源與基片間距的影響
蒸發源與基片間距會對薄膜均勻性等導致必定影響,按照實質鍍膜經驗,蒸發源與基片間距較小的狀況下,薄膜厚度相對更大,均勻性亦相對更好。因此呢在實質鍍膜生產中,咱們需要思慮怎樣恰當調節蒸發源與基片的間距,保證各區域的基片與蒸發源間距Z佳。
綜上所述,區別方式的蒸鍍工藝,區別蒸鍍時間,區別原料狀態,以及蒸發源與基片間距,都會對蒸鍍質量帶來必定影響。因此呢需要在蒸鍍過程中選擇Z為適合的原料和工藝方式。
移動終端中的真空鍍膜應用 手機背板裝飾鍍因為5G更加多的采用了高頻信號,對高頻信號屏蔽顯著的金屬(導電)手機背板材料確定退出了市場舞臺,取而代之的是玻璃背板和陶瓷背板。因為沒法運用傳統的陽極氧化鋁合金染色工藝,光學裝飾鍍作為玻璃染色的首選工藝。而陶瓷背板亦將磁控濺射做為印制logo、裝飾條紋的首選方法。電磁屏蔽膜5G時代Massive MIMO天線數量多,高頻高速趨勢顯著,對電磁屏蔽需要進一步加強[7] 。電磁屏蔽膜重點以卷繞式磁控濺射方式生產。LPCVD(Low Pressure CVD)
LPCVD重點指氣壓在Torr數量級的氣壓下,以掌控產率方式出現反應,相比APCVD,供給了更好的臺階覆蓋性和更高純度,在0.25-2Torr下一般用于制備化合物半導體、金屬化和鈍化層 ,20Torr周邊多運用硅烷沉積非晶硅。PECVD(Plasma Enhanced CVD)
PECVD能夠認為是LPCVD的一種,在LPCVD的環境下,運用等離子體來活化前驅體,能夠使CVD在低溫下(250℃~350℃)生成薄膜。一方面熱損失少,一方面控制了氣體和襯底材料之間的反應,同期亦能夠適用于不耐高溫的材料。詳細細分又能夠分為微波PECVD和射頻PECVD等。初期該技術曾經被叫作作“輝光放電沉積”,后又被叫作作“等離子體CVD”,最后定名為PECVD(Plasma Enhanced CVD)或PACVD(Plasma assisted CVD)。該技術最早由M. Berthelot在1869年提出設想,1953年H. Schmellenmeier 就用該技術制備了DLC涂層。熱絲CVD(Hot Filament CVD/Hot Wire CVD/Cat-CVD)
熱絲CVD常用于沉積高分子薄膜,將單體蒸發后在基片表面冷卻聚合。熱絲CVD亦被用于沉積DLC,重點的前驅體為甲烷等碳氫化合物。ALD(Atomic Layer Deposition)ALD能夠認為是LPCVD的一種,然則ALD與傳統化學氣相沉積(CVD)技術區別的是,所用的氣相前驅體經過交替脈沖的方式進入反應腔,前驅體彼此在氣相中不相遇,經過惰性氣體(Ar、N2)沖洗隔開并實現前驅體在基片表面的單層飽和吸附反應。其反應屬于自限制性反應,即當一種前驅體與另一種前驅體反應達到飽和時,反應自動終止?;谠訉由L的自限制性特點,以原子層沉積制備的薄膜擁有優異的厚度掌控性能,能夠經過掌控脈沖的周期數來精確的掌控薄膜生長的厚度。在具備高深寬比結構(如深孔)的物質表面,ALD辦法亦擁有最好的臺階覆蓋性。因為前驅體是經過交替脈沖的方式進入反應腔,原子層沉積中,薄膜的生長是以一種周期性的方式進行的。一個周期包含四個周期:第1種前驅體蒸汽通入反應腔體;惰性氣體沖洗;第二種前驅體蒸汽通入反應腔體;惰性氣體沖洗。每一個周期薄膜生長必定的厚度,經過掌控這種周期的次數能夠得到所需厚度的薄膜。濺射鍍膜(Sputtering)
濺射鍍膜做為一種非常有效的薄膜沉積辦法,被廣泛和成功地應用于許多方面。其特點可歸納為:可制備成靶材的各樣材料均可做為薄膜材料,包含各樣金屬、半導體、鐵磁材料,以及絕緣的氧化物、陶瓷、聚合物等物質,尤其適合高熔點和低蒸氣壓的材料沉積鍍膜;可經過多元靶材一起濺射的方式形成化合物薄膜;經過掌控氣壓、濺射功率,基本上能夠得到穩定的沉積速率;進一步經過掌控鍍膜時間,容易得到均勻的高精度的膜厚,且重復性好;基片與膜的附著強度是通常蒸鍍膜的10倍以上,且因為濺射粒子帶有高能量,在成膜面會繼續表面擴散得到硬且致密的薄膜,同期高能量使基片只要較低的溫度就可結晶;薄膜形成初期成核密度高,能夠產生厚度10nm以下的極薄連續膜。因為磁控濺射鍍膜的以上特性,其被廣泛的用于制備超硬膜、耐腐蝕摩擦薄膜、超導薄膜、磁性薄膜、光學薄膜以及微電子薄膜(集成電路中晶體管的金屬電極層),逐步作為了制造許多制品的一種常用手段,并在近期十幾年,發展出一系列新的濺射技術。在光學行業產生了對靶濺射、反應濺射(分區氧化或射頻離子源反應濺射)、離子源直接濺射等適用與區別精度的工藝,而在工具鍍行業的最重點發展是HIPIMS技術部分處理了磁控濺射制造工具鍍層速度太慢的問題,以及VEECO發明了離子束濺射辦法。磁控濺射沉積的重點優良有:
①粒子能量高,得到的薄膜結構致密穩定,不會顯現電子束熱蒸發鍍膜顯現的波長漂移等現象;
②因為能夠設置為滾筒式磁控濺射,能夠用真空腔的圓柱側表面積來衡量可鍍面積,在較低的沉積速率下,在手機裝飾鍍等行業得到了比蒸發鍍膜更高的生產效率;
③濺射相較于蒸發膜層折射率穩定,因此呢能夠運用鍍膜時間來掌控膜層的光學厚度。
④得到致密膜層無需對薄膜進行加熱,適用于PET膜等耐溫不超過100℃的材料。
⑤工藝一旦調成重復性非常高;
磁控濺射的缺點重點是:
①成膜的沉積速率要小于蒸發鍍膜(然則如以上被可鍍面積彌補);
②射出粒子能量高,形成薄膜應力大,不適合于塑膠鏡片(常用材料為PC)等較為柔軟的基材。
③設備結構相對繁雜,價格較為昂貴。
④濺射鍍膜相對蒸發鍍膜而言工程師基本較差,非常多“鍍膜師傅”有蒸發機經驗而無濺射機經驗。
LeyboldHelios原理圖
電弧/多弧離子鍍(Arc Vapor Deposition)
電弧離子鍍是一種利用電極放電產生電弧,從而使膜材氣化的鍍膜手段,最早的工業化應用在1970s發源于前蘇聯,后來在1980s在西方國家亦得到應用 。在電弧離子鍍中,電弧產生的高溫快速的將待鍍物質氣化成份子團和液滴,而后在強電場下電離并飛往被鍍物,形成鍍層。根據拉弧方式能夠將電弧離子鍍分為真空電?。╒acuum Arc)、陰極?。–atholic)離子鍍、陽極?。ˋnodic)離子鍍和高氣壓電?。℅aseous Arc)。高氣壓電?。℅aseous Arc)常常用于噴涂、焊接和電火花鍍(一種電火花強化辦法)中。
電子束蒸發鍍膜原理
電子束蒸發是一種理學氣相沉積 (PVD)技術,它在真空下利用電子束直接加熱蒸發材料(一般是顆粒),并將蒸發的材料傳送到基板上形成一個薄膜。電子束蒸鍍能夠鍍出高純度、高精度的薄膜。
電子束蒸發工作流程
電子束蒸發是基于鎢絲的蒸發。大約 5 到 10 kV 的電流經過鎢絲(位置于沉積區域外以避免污染)并將其加熱到出現電子熱離子發射的點。運用永磁體或電磁體將電子聚焦并導向蒸發材料(安置在坩堝中)。在電子束撞擊蒸發丸表面的過程中,其動能轉化為熱量,釋放出高能量(每平方英寸數百萬瓦以上)。因此呢,容納蒸發材料的爐床必須水冷以避免熔化。
電子束蒸發優點和缺點
電子束蒸發能夠蒸發高熔點材料,比通常電阻加熱蒸發效率更高。電子束蒸發可廣泛用于高純薄膜和導電玻璃等光學鍍膜。它還擁有用于航空航天工業的耐磨和熱障涂層、切削和工具工業的硬涂層的潛在工業應用。然而,電子束蒸發不可用于涂覆繁雜幾何形狀的內表面。另外,電子槍中的燈絲退化可能引起蒸發速率不均勻。
電子束蒸發應用
電子束蒸發因其高沉積速率和高材料利用效率而被廣泛應用于各樣應用中。例如,高性能航空航天和汽車行業,對材料的耐高溫和耐磨性有很高的需求;耐用的工具硬涂層;和化學屏障和涂層,以守護腐蝕環境中的表面。電子束蒸發亦用于光學薄膜,包含激光光學、太陽能電池板、玻璃和建筑玻璃,以賦予它們所需的導電、反射和透射特性。
電子束蒸發VS熱蒸發
電子束蒸發與熱蒸發最大的區別在于:電子束蒸發是用一束電子轟擊物體,產生高能量進行蒸發, 熱蒸發經過加熱完成這一過程。與熱蒸發相比,電子束蒸發供給了高能量;但將薄膜的厚度掌控在 5nm 量級將是困難的。在這種狀況下,帶有厚度監控器的良好熱蒸發器將更合適。
與熱蒸發相比,電子束蒸發擁有許多優點
電子束蒸發能夠將材料加熱到比熱蒸發更高的溫度。這準許高溫材料和難熔金屬(例如鎢、鉭或石墨)的非常高的沉積速率和蒸發。
電子束蒸發能夠沉積更薄、純度更高的薄膜。坩堝的水冷將電子束加熱嚴格限制在僅由源材料占據的區域,從而消除了相鄰組件的任何不必要的污染。
電子束蒸發源有各樣尺寸和配置,包含單腔或多腔。
磁控濺射鍍膜技術與原理
磁控濺射技術得以廣泛的應用,是由于該技術有別于其它鍍膜辦法的特點所決定的。其特點可歸納為:可制備成靶材的各樣材料均可做為薄膜材料,包含各樣金屬、半導體、鐵磁材料,以及絕緣的氧化物、陶瓷等物質,尤其適合高熔點和低蒸汽壓的材料沉積鍍膜在適當要求下多元靶材共濺射方式,可沉積所需組分的混合物、化合物薄膜;在濺射的放電氣中加入氧、氮或其它活性氣體,可沉積形成靶材物質與氣體分子的化合物薄膜;掌控真空室中的氣壓、濺射功率,基本上可得到穩定的沉積速率,經過精確地掌控濺射鍍膜時間,容易得到均勻的高精度的膜厚,且重復性好;濺射粒子幾乎不受重力影響,靶材與基片位置可自由安排;基片與膜的附著強度是通常蒸鍍膜的10倍以上,且因為濺射粒子帶有高能量,在成膜面會繼續表面擴散而得到硬且致密的薄膜,同期高能量使基片只要較低的溫度就可得到結晶膜;薄膜形成初期成核密度高,故可生產厚度10nm以下的極薄連續膜。
磁控濺射工作原理:
磁控濺射屬于輝光放電范疇,利用陰極濺射原理進行鍍膜。膜層粒子源自于輝光放電中,氬離子對陰極靶材產生的陰極濺射功效。氬離子將靶材原子濺射下來后,沉積到元件表面形成所需膜層。磁控原理便是采用正交電磁場的特殊分布掌控電場中的電子運動軌跡,使得電子在正交電磁場中變成為了擺線運動,因而大大增多了與氣體分子碰撞的幾率。濺射機理:
用高能粒子(大都數是由于電場加速的氣體正離子)撞擊固體表面(靶),使固體原子(分子)從表面射出的現象叫作為濺射。濺射現象很早就為人們所認識,經過前人的海量實驗科研,咱們對這一重要理學現象得出以下幾點結論:(1)濺射率隨入射離子能量的增多而增大;而在離子能量增多到必定程度時,因為離子注入效應,濺射率將隨之減小;(2)濺射率的體積與入射粒子的質量相關:(3)當入射離子的能量小于某一臨界值(閥值)時,不會出現濺射;(4)濺射原子的能量比蒸發原子的能量大許多倍;(5)入射離子的能量很低時,濺射原子角分布就不完全符合余弦分布規律。角分布還與入射離子方向相關。從單晶靶濺射出來的原子趨向于集中在晶體密度最大的方向。(6)由于電子的質量很小,因此即使運用擁有極高能量的電子轟擊靶材亦不會產生濺射現象。因為濺射是一個極為繁雜的理學過程,觸及的原因非常多,長時間敗興針對濺射機理雖然進行了非常多的科研,提出過許多的理論,但都難以完善地解釋濺射現象。輝光放電:
輝光放電是在真空度約為一的稀薄氣體中,兩個電極之間加上電壓時產生的一種氣體放電現象。濺射鍍膜基于荷能離子轟擊靶材時的濺射效應,而全部濺射過程都是創立在輝光放電的基本之上的,即濺射離子都源自于氣體放電。區別的濺射技術所采用的輝光放電方式有所區別,直流二極濺射利用的是直流輝光放電,磁控濺射是利用環狀磁場掌控下的輝光放電。當電壓繼續上升時,離子與陰極之間以及電子與氣體分子之間的碰撞變得重要起來。在碰撞趨于頻繁的同期,外電路轉移給電子與離子的能量亦在逐步增多。一方面,離子針對陰極的碰撞將使其產生二次電子的發射,而電子能量亦增多到足夠高的水平,它們與氣體分子的碰撞起始引起后者出現電離,如圖(a)所示。這些過程均產生新的離子和電子,即碰撞過程使得離子和電子的數目快速增多。此時,隨著放電電流的快速增多,電壓的變化卻不大。這一放電周期叫作為湯生放電。
在湯生放電周期的后期,放電起始進入電暈放電周期。此時,在電場強度較高的電極尖端部位起始顯現有些跳躍的電暈光斑。因此呢,這一周期叫作為電暈放電。
在湯生放電周期之后,氣體會忽然出現放電擊穿現象。此時,氣體起始具備了相當的導電能力,咱們將這種具備了必定的導電能力的氣體叫作為等離子體。此時,電路中的電流大幅度增多,同期放電電壓卻有所下降。這是因為此時的氣體被擊穿,因而氣體的電阻將隨著氣體電離度的增多而明顯下降,放電區由原來只集中于陰極邊緣和不規則處變成向全部電極表面擴展。在這一周期,氣體中導電粒子的數目海量增多,粒子碰撞過程伴同的能量轉移亦足夠地大,因此呢放電氣體會發出顯著的輝光。
電流的繼續增多將使得輝光區域擴展到全部放電長度上,同期,輝光的亮度持續加強。當輝光區域充滿了兩極之間的全部空間之后,在放電電流繼續增多的同期,放電電壓又開始提升。以上的兩個區別的輝光放電周期常被叫作為正常輝光放電和反常輝光放電周期。反常輝光放電是通常薄膜濺射或其他薄膜制備辦法經常采用的放電形式,由于它能夠供給面積很強、分布較為均勻的等離子體,有利于實現大面積的均勻濺射和薄膜沉積。
磁控濺射:
平面磁控濺射靶采用靜止電磁場,磁場為曲線形。其工作原理如下圖所示。電子在電場功效下,加速飛向基片的過程中與氫原子出現碰撞。若電子擁有足夠的能量(約為30eV)。時,則電離出Ar+并產生電子。電子飛向基片,Ar+在電場功效下加速飛向陰極濺射靶并以高能量轟擊靶表面,使靶材出現濺射。在濺射粒子中,中性的靶原子(或分子)沉積在基片上形成薄膜。二次電子e1在加速飛向基片時受磁場B的洛侖茲力功效,以擺線和螺旋線狀的復合形式在靶表面作圓周運動。該電子e1的運動路徑不僅很長,況且被電磁場捆綁在靠近靶表面的等離子體區域內。在該區中電離出海量的Ar+用來轟擊靶材,因此呢磁控濺射擁有沉積速率高的特點。隨著碰撞次數的增多,電子e1的能量逐步降低,同期,e1逐步遠離靶面。低能電子e1將如圖中e3那樣沿著磁力線來回振蕩,待電子能量將耗盡時,在電場E的功效下最后沉積在基片上。因為該電子的能量很低,傳給基片的能量很小,使基片溫升較低。在磁極軸線處電場與磁場平行,電子e2將直接飛向基片。然則,在磁控濺射安裝中,磁極軸線處離子密度很低,因此e2類電子很少,對基片溫升功效不大。
磁控濺射工作原理圖
磁控濺射的基本原理便是以磁場改變電子運動方向,捆綁和延長電子的運動路徑,加強電子的電離概率和有效地利用了電子的能量。因此呢,在形成高密度等離子體的反常輝光放電中,正離子對靶材轟擊所導致的靶材濺射更加有效,同期受正交電磁場的捆綁的電子只能在其能量將要耗盡時才可沉積在基片上。這便是磁控濺射擁有“低溫”、“高速”兩大特點的機理。
磁控濺射的應用:
磁控濺射的優點:
(1)操作易控。鍍膜過程,只要保持工作壓強、電功率等濺射要求相對穩定,就能得到比較穩定的沉積速率。
(2)沉積速率高。在沉積大部分的金屬薄膜,尤其是沉積高熔點的金屬和氧化物薄膜時,如濺射鎢、鋁薄膜和反應濺射TiO2、ZrO2薄膜,擁有很高的沉積率。
(3)基板低溫性。相對二極濺射或熱蒸發,磁控濺射對基板加熱少了,這一點對實現織物的上濺射相當有利。
(4)膜的牢靠性好。濺射薄膜與基板有著極好的附著力,機械強度亦得到了改善。
(5)成膜致密、均勻。濺射的薄膜聚集密度廣泛加強了。從顯微照片看,濺射的薄膜表面微觀形貌比較精致細密,況且非常均勻。
(6)濺射的薄膜均擁有優異的性能。如濺射的金屬膜一般能得到良好的光學性能、電學性能及某些特殊性能。
(7)易于組織大批量生產。磁控源能夠按照需求進行擴大,因此呢大面積鍍膜是容易實現的。再加上濺射可連續工作,鍍膜過程容易自動掌控,因此呢工業上流水線作業完全作為可能。
(8)工藝環保。傳統的濕法電鍍會產生廢液、廢渣、廢氣,對環境導致嚴重的污染。不產生環境污染、生產效率高的磁控濺射鍍膜法則可較好處理這一困難。
磁控濺射應用:
磁控濺射日前是一種應用非常廣泛的薄膜沉積技術,濺射技術上的持續發展和對新功能薄膜的探索科研,使磁控濺射應用延伸到許多生產和研究行業。
(1)在微電子行業做為一種非熱式鍍膜技術,重點應用在化學氣相沉積(CVD)或金屬有機化學氣相沉積(MOCVD)生長困難及不適用的材料薄膜沉積,況且能夠得到大面積非常均勻的薄膜。包含歐姆接觸的Al、Cu、Au、W、Ti等金屬電極薄膜及可用于柵絕緣層或擴散勢壘層的TiN、Ta2O5、TiO、Al2O3、ZrO2、AlN等介質薄膜沉積。
(2)磁控濺射技術在光學薄膜(如增透膜)、低輻射玻璃和透明導電玻璃等方面亦得到應用。在透明導電玻璃在玻璃基片或柔性襯底上,濺射制備SiO2薄膜和摻雜ZnO或InSn氧化物(ITO)薄膜,使可見光范圍內平均光透過率在90%以上。
(3)在現代機械加工工業中,利用磁控濺射技術制作表面功能膜、超
硬膜,自潤滑薄膜,能有效的加強表面硬度、復合韌性、耐磨損性和抗高溫化學穩定性能,從而大幅度地加強涂層制品的運用壽命。
磁控濺射除以上已被海量應用的行業,還在高溫超導薄膜、鐵電體薄膜、巨磁阻薄膜、薄膜發光材料、太陽能電池、記憶合金薄膜科研方面發揮重要功效。
磁控濺射技術因為其明顯的優點作為工業鍍膜重點技術之一。在將來的科研中,新技術向工業行業的推廣、磁控濺射技術與計算機的結合已作為一個科研方向,怎樣利用計算機來掌控精確鍍膜過程,利用計算機來模擬鍍膜時的磁場、溫度場、以及氣流分布,必將能給濺射鍍膜過程供給靠譜的數據支持,亦是經濟有效的辦法。
光學鍍膜典型舉例1:寶石鍍膜
“鍍膜處理”是一種表面處理技術,用沉淀技術、噴鍍技術等在寶石表面鋪設多層分子或原子膜,能夠改善其外觀面貌。此刻的“鍍膜處理”技術已然較為成熟,在珠寶玉石中亦顯現的較多,不少商家亦利用這一點包裝出非常多“珠寶”詐騙不認識行情的消費者。
鍍膜托帕石
鍍膜水晶
照片源自:米玲麗,2020
咱們常說的“水色氣息”便是指在無色托帕石表面“鍍膜處理”所產生的五彩斑斕的視覺效果。
“鍍膜處理”重點改變寶石的那些特征
“鍍膜處理”重點是為了改善寶石的顏色和表面光潔度,加強寶玉石的光澤。在寶石表面鍍上有色膜,能夠直接改善或加強寶玉石的顏色,同期薄膜層的干涉功效亦能夠使寶石產生美麗的顏色。另外,膜層亦會掩蓋寶石表面凹坑、裂隙、擦痕等缺陷,加強表面光潔度。
那些寶石品質頻繁運用“鍍膜處理”
非常多種寶玉石都能夠用“鍍膜處理”的方式來改善其顏色或光澤,平常的有托帕石、坦桑石、水晶、碧璽等。
如上圖中這5顆0.39-0.82克拉的坦桑石在反射光下觀察到的下腰刻面比亭部主刻面的未涂層部分表示出更高的光澤。連接處和有些小的缺口區域已磨損,露出下面坦桑石不太飽和的紫色。
照片源自:GIA
還有法國寶石學實驗室(LFG)看到的第1個用彩色薄膜覆蓋的合成云紋石的例子。在顯微鏡下,這些薄片表示出金屬光澤,粉紅色似乎集中在表面。因為這層薄膜的劃痕,觀察到顏色不均勻。
照片源自:GIA
在水晶的表面鍍上一層彩膜,使水晶產生暈彩效應,這般看起來更好看,商家亦就有了更大的炒作噱頭。
鍍膜水晶
照片源自:Google
眾所周知,碧璽被叫作為“落入凡間的彩虹”,而有些不良商家為了能夠節約成本,經常會將有些淺色或無色的碧璽進行鍍膜處理,以此來牟取暴利!鍍了膜的碧璽表面不會有太自然的暈彩效應,跟天然碧璽比起來相差甚遠。
托帕石的“鍍膜處理”工藝已很成熟,鍍膜后的托帕石可產生紅、黃、綠、紫、藍等各樣各樣的顏色,鍍膜托帕石日前分三代制品。
照片源自:李瑞璐,2011
第1代
第1代制品技術為直接噴鍍氧化物薄膜法,即在低溫要求下,將金屬氧化物噴鍍在托帕石基體上,因為膜層折射率與托帕石基體折射率區別,膜層與托帕石相互功效產生光學干涉現象,使得鍵膜托帕石呈現帶有綠色和紫色的多彩色。
照片源自:李瑞璐,2011
第二代
第二代鍍膜制品技術較直接鍍膜更為精細,膜層為交替層結構,會產生的光學干涉濾波對光有選取吸收性,使鍍膜托帕石產生顏色。此類鍍膜托帕石用入射光觀察,鍵膜表面可呈現出金黃色。
第三代
第三代制品亦叫作為TCF托帕石,該“TCF”技術指的是“熱熔”技術(Thermalcolorfusion),是近年來興起的一種新型的寶石優化處理技術,它是在原鍍膜工藝的基本上增多了擴散處理技術。
照片源自:王海燕,2009
即先將氧化物或和金屬單質或摻雜劑噴鍍或沉積在托帕石基體表面,而后進行高溫熔結處理,因此TCF托帕石的耐久性亦很強,并且TCF技術使得托帕石制品的顏色非常豐富,并且鮮艷逼真,柔和自然。TCF托帕石的缺點是粒度太小,不足1克拉。
快速鑒別“鍍膜處理”
通常來講,肉眼及放大觀察會發掘“水色氣息”表面光澤反常,針劃會留下痕跡,膜層脫落。借用有些常規的鑒定儀器會發掘寶石折射率、多色性、吸收光譜反常。另一,對包鑲首飾要格外留意,必定要取下后觀察。
照片源自:米玲麗,2020
但肉眼與簡單儀器鑒定難度很強,要得到科學的結果,必定要找經過專業的顯微鏡觀察、經過儀器分析等才可得出準確結論。
光學鍍膜典型舉例2:光學濾光片
濾光片核心參數
中心波長
中心波長(CWL)一般用于暗示帶通濾光片的峰值透射率,或是陷波濾光片的峰值反射率。然而,這個術語常被誤用 -CWL實質上定義為在峰值透射率為50%的波長之間的中點,叫作為半峰 全寬(FWHM)。干涉濾光片的峰值則一般不會位置于波長中點。請參閱圖1關于CWL和FWHM的說明。
帶寬
帶寬是一個波長范圍,用于暗示頻譜經過入射能量穿過濾光片的特定部分。帶寬又叫作為FWHM(圖1)。
圖 1: 中心波長和半峰全寬說明
截止范圍
阻斷范圍是用于暗示經過濾光片衰減的能量光譜區域的波長間隔(圖2)。阻斷程度一般會在光密度中指定。
圖 2: 截止范圍說明
光密度
光密度(OD)描述濾光片阻斷規格,并且與穿過的能量透射量相關(方程式1–2)。高光密度值暗示非常低的透射率,低光密度則暗示高透射率。圖3描述了三種區別的光密度:OD 1.0,OD 1.3和OD 1.5表示越高的OD值的透射率越低。
圖 3: 光密度說明
二向色性濾光片
二向色性濾光片是用于取決于波長透射率或反射光的濾光片類型;特定波長范圍透射的光則鑒于區別范圍的光線反射或吸收(圖4)。二向色性濾光片常用于長波通和短波通應用。
圖 4: 二向色性濾光片鍍膜說明
初始波長
初始波長是用于暗示在長波通濾光片中透射率增多至50%波長的術語。初始波長由圖5中的λcut-on初始暗示。
圖 5: 初始波長說明
光學濾光片制造技術
吸收性和二向色性濾光片
范圍廣泛的可分成兩大類:吸收性和二向色性。兩者的區別不在于它過濾什么,而是怎樣濾光。吸收性濾光片的光線阻斷以玻璃基片的吸收特性為基本。換句話說,被阻斷的光線不會反射回濾光片;相反的,光線被它吸收且包括在濾光片內。在系統內多余的光線形成噪音的問題時,吸收性濾光片是理想的選取。吸收性濾光片亦擁有方向不敏銳的額外功能;光線可從各樣方向入射濾光片且濾光片將保持其透射和吸收特性。
相反的,二向色性濾光片的運作是反射多余的波長并透射所需的頻譜部分。在有些應用中,這是一個需要的效果,由于光能夠經過波長掰開為兩個源自。這可經過增多單層或多層區別折射指數的材料完成干涉光波性質來實現。在干涉濾光片,光從較低折射率材料的移動將反射高折射率材料;僅有特定方向和波長的光將積極干涉傳入光束并穿過材料,而其他所有的光線將相消干涉并反射材料(圖7)。其他相關干擾的信息,請參閱“光學101:1級的理論基本”。
圖 7: 在玻璃基片上交替的高與低指標材料的多層沉積
與吸收性濾光片區別,二向色性濾光片擁有極高的方向敏銳。當用于任何方向的設計用途之外時,二向色性濾光片沒法滿足zui初標示的透射率和波長規格。經過二向色性濾光片加強入射角將使它移向較短的波長(即對藍波長);降低方向則會移向較長的波長(即對紅波長)。
探索二向色性帶通濾光片
帶通濾光片用于廣泛的行業,能夠是二向色性或彩色基片。二向色性帶通濾光片是由于兩種區別的技術制造的:傳統和加硬濺射法,或鍍加硬膜。這兩種技術經過在玻璃基片上交替的高與低折射率材料的多層沉積實現其獨特的透射率和反射特性。事實上,按照應用的區別,在特定基片上每面可能有超過100層材料沉積。
傳統鍍膜濾光片和加硬濺射法濾光片之間的差別是基片層數。在傳統鍍膜帶通濾光片,區別的指標材料層沉積在多個基片上而后再夾在一塊。例如,假設圖7中的照片重復疊加乃至超過100倍。這個技術引起降低透射率的厚濾光片。透射的減少是因為入射光穿過并經過數個基片層被吸收和/或反射所引起的。相反的,在加硬濺射法帶通濾光片,區別的指標材料只沉積在單個基片上 圖8)。這個技術引起高透射率的薄濾光片。相關制造技術的其他信息,請參閱“光學鍍膜簡介”。請查看硬鍍膜的好處,幫忙您選取適合應用的濾光片。
圖 8: 傳統濾光片(左)和加硬濺射法濾光片(右)
光學鍍膜技術和裝備
光學薄膜是現代光學和光電系統最重要的構成部分,在光通信、光學表示、激光加工、激光核聚變等高科技及產業行業已然作為核心元器件,其技術突破常常作為現代光學及光電系統加速發展的主因。
光學薄膜的技術性能和靠譜性,直接影響到應用系統的性能、靠譜性及成本。如圖1是光通訊技術中運用窄帶濾光片調制區別的通訊通道示意圖。圖 2是激光核聚變系統中海量運用到的薄膜元器件。
圖1 光通訊系統中經過WDM濾光片系統調控區別波長示意圖
圖2 美國NIF高功率激光系統中的光學結構示意圖,其中海量運用到傳輸鏡、偏振膜等光學薄膜元器件
隨著行業的持續發展,精細光學系統對光學薄膜的光譜掌控能力和精度需求越來越高,而消費電子對光學薄膜器件的需要更強調超大的量產規模和普通公眾的易用和舒適性。
重點光學鍍膜技術和裝備發展光學鍍膜技術在過去幾十年實現了長足的發展,從舟蒸發、電子束熱蒸發及其離子束輔助沉積技術發展到離子束濺射和磁控濺射技術。近年來在這些沉積技術和裝備行業的重點技術發展包含:1
間歇式直接光控(intermittent measuring method)間歇式直接光控(intermittent measuring method):以Leybold Optics機構的OMS5000系統為表率,光學鍍膜過程中越來越多地運用間歇式信號采集系統,對鍍膜過程制品片實現直接監控。相針對間接光控和晶控系統,間歇式直接光控系統有利于降低實質制品上的薄膜厚度分布誤差,能夠進一步加強制品良率并減少了工藝調試時間。
圖3 Leybold Optics 機構OMS5000的間歇式直接光控系統
漸變折射率結構薄膜技術與裝備(Rguate filter and Coater)漸變折射率結構薄膜技術與裝備(Rguate filter and Coater):已然有海量科研工作已然證實Rugate無界面型薄膜結構和準Rugate多種折射率薄膜結構經過加強調制折射率在薄膜厚度方向上分布,能設計出非常繁雜的光譜性能,(部分)消除了薄膜界面特征,(部分)消除界面效應,如電磁波在界面上比薄膜內部更高密度的吸收中心和散射,亦能夠增多了薄膜力學穩定性。
漢諾威激光工程中心的數據表示(圖4),(準)Rugate薄膜結構與傳統的高低折射率光學薄膜結構相比,能夠擁有更高的抗激光損害閾值。如Rugate Filter 設計,其1064 nm 10 ns 1000發零損害幾率能夠做到100 J/cm2以上。
圖4 高低折射率結構和(準)Rugate薄膜結構的抗激光損害閾值對比測試結果
圖5所示為德國CEC機構研發的靶面掃描共濺系統。經過在離子束濺射鍍膜過程中,精確掃描兩種材料拼接而成的混合濺射靶,能夠實現折射率的漸變結構,高精度制備(準)Rugate復合薄膜結構的光學薄膜,得到比高低折射率薄膜結構更繁雜的光譜性能和更優異的附著力、應力等理學性能。
圖5德國CEC機構靶面掃描共濺系統
磁控濺射光學鍍膜系統(Magnetron Sputtering)
以Leybold Helios和Shincron RAS為表率,磁控濺射技術及裝備在精細光學行業和消費光電子薄膜行業占據越來越大的份額。磁控濺射薄膜沉積過程掌控簡單,粒子能量高,得到的薄膜結構致密穩定。
圖6是Helios的基本結構和原理,其采用非常緊湊的板式開合結構,真空室空間利用率非常高,整體結構亦非常緊湊。其采用平面雙靶磁控濺射陰極和等離子體源一起實現化合物薄膜的快速沉積過程,能夠用于介質干涉濾光片(氧化物、氮化物)、共濺射(摻雜,混合折射率薄膜)、金屬膜 (Cr,Ag,Al…)及金屬介質干涉濾光片。其裝卡系統能夠實現真空室處在真空狀態下快速進出制品,為全部系統的穩定性奠定了重要基本??偟?span style="color: green;">來講,該設備非常適合應用于中小批量的精細光學元件鍍膜。
圖6 LeyboldOpitcs Helios磁控濺射光學鍍膜系統(上),基本結構與原理圖(下)
光學鍍膜中平常的不良分析與改善對策
鍍膜制品的平常問題,部分是鍍膜工序的本身導致的,部分是前工程遺留的問題,鍍膜終的品質是全部光學零件加工的(尤其是拋光、清洗)的綜合反映,針對顯現鍍膜不良時必須綜合思慮,才可真正找到不良產生的原由,對策改善才可取得成效。
膜臟(亦叫作白壓克)顧名思義,膜層有臟。通常的膜臟出現在膜內或膜外。臟能夠包含:灰塵點、白霧、油斑、指紋印、口水點等。(灰塵點和白霧單列)灰點臟現象:鏡片膜層表面或內部有有些點子(不是膜料點)有些能夠擦除,有的不能擦除。并且會有點狀脫膜產生。
產生原由:
1、真空室臟,在起始抽真空時的空氣渦流將真空室底板、護板的臟灰帶到鏡片上,形成灰點層。(膜內,不可擦除,會有點狀脫膜)
2、鏡圈或碟片臟,有浮點灰塵,在離子束功效下附著到了鏡片上形成灰點層。(膜內,不可擦除,會有點狀脫膜)
3、鏡片上傘時就有灰塵點,上傘時無檢測挑選。(膜內,不可擦除,會有點狀脫膜)
4、鍍制完成后的環境污染是膜外灰點的重點成因,尤其是當鏡片熱的時候,更易吸附灰塵,況且難以擦除。(膜外)
5、真空室充氣口環境臟、起始充氣量過大、充氣過濾器臟,充氣時鏡片溫度過高亦是導致鏡片膜外灰塵點不良的原由。(膜外)
6、 作業員人為帶來的灰塵污染(膜內膜外)
7、 工作環境中灰塵太多
改善思路:杜絕灰塵源
改善對策:
1、工作環境改造潔凈車間,嚴格按潔凈車間規范實施。
2、盡可能做好環境衛生。盡可能利用潔凈工作臺。
3、 真空室周期打掃,保持清潔。
膜外白霧
現象:鍍膜完成后,表面有有些淡淡的白霧,用丙酮或混合液擦拭,會有越擦越嚴重的現象。用氧化鈰粉擦拭,能夠擦掉或減輕,(又叫作:可擦拭壓克)
分析:膜外白霧的成因較為繁雜,可能的成因有:
①、膜結構問題:外層膜的柱狀結構松散,外層膜太粗糙;
②、蒸發角過大,膜結構粗糙。
③、溫差:鏡片出罩時內外溫差過大
④、潮氣;鏡片出罩后擺放環境的潮氣
⑤、真空室內Polycold解凍時水汽過重
⑥、蒸鍍中充氧不完全,膜結構不均勻
⑦、膜與膜之間的應力
改善思路:膜外白霧成因非常多,但各有些特征,盡可能對癥下藥。重點思路,一是把膜做的致密光滑些不易吸附,二是改善環境減少吸附的對象。
改善對策:
1、改善膜系,外層加二氧化硅,使膜表面光滑,很難吸附。改善鏡片出罩時的環境(干燥、清潔)
2、降低出罩時的鏡片溫度(延長在真空室的冷卻時間)減少溫差、降低應力。
3、改善充氧(加大),改善膜結構。
4、適當降低蒸發速率,改善柱狀結構
5、離子輔助鍍膜,改善膜結構
6、加上polycold解凍時的小充氣閥(其功能是即時帶走水汽)
7、從蒸發源和夾具上想辦法改善蒸發角。
8、改善基片表面粗糙度。
9、重視polycold解凍時的真空度。
膜內白霧
白霧形成在膜內,沒法用擦拭辦法祛除。
可能的成因:
①、基片臟,附著前工程的殘留物
②、鏡片表面腐蝕污染
③、膜料與膜料之間、膜料與基片之間的不匹配。
④、氧化物充氧不足。
⑤、一層氧化鋯膜料,可能對某些基片產生白暈現象
⑥、基片進罩前(洗凈后)受潮氣污染
⑦、洗凈或擦拭不良,洗凈痕跡、擦拭痕跡
⑧、真空室臟、水氣過重
⑨、環境濕度大
改善思路:基片本身的問題可能是重點的,鍍膜是盡可能彌補,鍍膜本身的可能是膜料匹配問題。
改善對策:
1、改進膜系,層不消氧化鋯。
2、盡可能減少真空室開門時間,罩與罩之間在短期內做好真空室的清潔、鍍膜準備工作。
3、真空室在更換護板、清潔后,能空罩抽真空烘烤一下,更換的護板等真空室部件必須干燥、干凈。
4、改善環境
5、妥善守護進罩前在傘片上的鏡片,免受污染。
6、改善洗凈、擦拭效果。
7、改善膜匹配(思慮層用Al2O3)
8、改善膜充氧和蒸發速率(降低)
9、加快前工程的流程。前工程對已加工光面的守護加強。
十、拋光加工完成的光面,必須立即清潔干凈,不可有拋光粉或其他雜質附著干結。
PVD 鍍膜材料——靶材知識
PVD 鍍膜材料概述
PVD 鍍膜材料重點用以制備各樣擁有特定功能的薄膜材料,應用行業包含平板表示、半導體、太陽能電池、光磁記錄媒介、 光學元器件、 節能玻璃、 LED、工具改性、高檔裝飾用品等。
(1)薄膜材料制備技術概述
薄膜材料生長于基板材料(如屏顯玻璃、光學玻璃等)之上,通常由金屬、非金屬、合金或化合物等材料經過鍍膜后形成,擁有增透、吸收、截止、分光、反射、濾光、干涉、守護、防水防污、防靜電、導電、導磁、絕緣、耐磨損、耐高溫、耐腐蝕、抗氧化、防輻射、裝飾和復合等功能,并能夠加強制品質量、環保、節能、延長制品壽命、改善原有性能等。
日前,薄膜材料制備技術重點包含:
理學氣相沉積(PVD)技術 和 化學氣相沉積(CVD)技術。①PVD技術
PVD 技術是制備薄膜材料的重點技術之一,指在真空要求下采用理學辦法,將某種物質表面氣化成氣態原子、分子或部分電離成離子,并經過低壓氣體(或等離子體)過程,在基板材料表面沉積擁有某種特殊功能的薄膜材料的技術。在PVD 技術下,用于制備薄膜材料的物質,統叫作為 PVD 鍍膜材料。
經太多年發展,PVD 技術已作為日前主流鍍膜辦法,重點包含濺射鍍膜 和真空蒸發鍍膜。
A、濺射鍍膜
濺射鍍膜指的是利用離子源產生的離子,在真空中經過加速聚集,而形成高速度的離子束流,轟擊固體表面,離子和固體表面原子出現動能交換,使固體表面的原子離開固體并沉積在基板材料表面的技術。被轟擊的固體是用濺射法沉積薄膜材料的原材料,叫作為濺射靶材。
通常來講,濺射靶材重點由靶坯、背板(或背管)等部分形成,其中,靶坯是高速離子束流轟擊的目的材料,屬于濺射靶材的核心部分,在濺射鍍膜過程中,靶坯被離子撞擊后,其表面原子被濺射飛散出來并沉積于基板上制成薄膜材料;因為濺射靶材需要安裝在專用的設備內完成濺射過程,設備內部為高電壓、高真空的工作環境,都數靶坯的材質較軟或高脆性,不適合直接安裝在設備內運用,因此呢,需與背板(或背管)綁定, 背板(或背管)重點起到固定濺射靶材的功效,且具備良好的導電、導熱性能。
濺射鍍膜的基本原理如下:
濺射鍍膜工藝可重復性好、膜厚可掌控,可在大面積基板材料上得到厚度均勻的薄膜,所制備的薄膜具有純度高、致密性好、與基板材料的結合力強等優點,已作為制備薄膜材料的重點技術之一,各樣類型的濺射薄膜材料已得到廣泛的應用,因此呢,對濺射靶材這一擁有高附加值的功能材料需要逐年增多,濺射靶材也已作為日前市場應用量最大的 PVD 鍍膜材料。
濺射靶材的種類較多,即使相同材質的濺射靶材亦有區別的規格。根據區別的歸類辦法,可將濺射靶材分為區別的類別,重點歸類狀況如下:
B、真空蒸發鍍膜
真空蒸發鍍膜指的是在真空要求下,利用膜材加熱安裝(叫作為蒸發源)的熱能,經過加熱蒸發某種物質使其沉積在基板材料表面的一種沉積技術。被蒸發的物質是用真空蒸發鍍膜法沉積薄膜材料的原材料,叫作之為蒸鍍材料。
真空蒸發鍍膜系統通常由三個部分組成:真空室、蒸發源或蒸發加熱安裝、安置基板及給基板加熱安裝。在真空中為了蒸發待沉積的材料,需要容器來支撐或盛裝蒸發物,同期需要供給蒸發熱使蒸發物達到足夠高的溫度以產生所需的蒸汽壓。
真空蒸發鍍膜的基本原理如下:
真空蒸發鍍膜技術擁有簡單便利、操作方便、成膜速度快等特點,是應用廣泛的鍍膜技術,重點應用于小尺寸基板材料的鍍膜。
②CVD技術
CVD 技術是在高溫下依靠化學反應、把含有形成薄膜元素的氣態反應劑或液態反應劑的蒸氣及反應所需其它氣體引入反應室,在襯底表面出現化學反應生成薄膜材料的技術。
2、重點PVD 鍍膜材料
(1)濺射靶材
濺射靶材是高速荷能粒子轟擊的目的材料,擁有高純度、高密度、多組元、晶粒均勻等特點,通常由靶坯和背板(或背管)構成。按運用的原材料材質區別,濺射靶材可分為金屬/非金屬單質靶材、合金靶材、化合物靶材等。
擁有表率性的濺射靶材制品如下:
濺射靶材應用于平板表示、光學元器件、節能玻璃、半導體、 太陽能電池等行業。表率性的濺射靶材圖示如下:
合金靶材:
(2)蒸鍍材料
采用區別的原材料、配方及工藝,迄今已開發出數百種蒸鍍材料,部分重點制品說明如下:
蒸鍍材料應用行業包含光學元器件、LED、平板表示和半導體分立器等。擁有表率性的蒸鍍材料圖示如下:
重點制品工藝流程
1、濺射靶材工藝流程
其中,重點工序的詳細含義如下:
粉末冶煉:對原料粉末進行前期的氣氛燒結,對原料粉末中氣體含量進行掌控。
粉末混合:靶材有著獨特的配方,需精確的掌控各組分的含量,并嚴格限制雜質含量,在粉末冶金的過程中,需要將各元素充分混合均勻,粒度分布均勻,防止污染,并要經過特殊工藝手段制備成混合型復合粉。
壓制成型:采用粉末冶金工藝制備的靶材需要對粉體材料進行預壓,使之作為中等密度生坯,其密度的均勻性和內部的缺陷影響著后期高溫燒結的成品率。
氣氛燒結:預壓成型的生坯需要再經過一次或多次的高溫燒結,按照區別材料選取區別的燒結溫度曲線,并選取區別的燒結環境,如燒結氣氛、燒結壓力等,從而制備成高密度的靶坯。
塑性加工:金屬坯錠需經過大幅度的塑性變形,以得到足夠的長寬厚度尺寸,并使得內部晶粒進行足夠的拉伸變形,從而在內部產生足夠多的位錯。? 熱處理:金屬坯錠在經過大幅度的塑形變形后,按照區別的材料的特性選取熱處理工藝,從而使金屬材料出現重結晶,去除材料內應力。
超聲探傷:靶坯加工完后需要采用超聲波進行檢測材料內部是不是有缺陷,靶坯與背板綁定完成后,需要采用水浸式超聲波掃描儀進行粘結層的檢測,檢驗粘結面積是不是達標。
機械加工:靶坯需要進行精細的機械成型加工,用于與靶坯復合運用的背板,因為承擔與鍍膜設備精確協同、承受高壓水冷等功效,需要具備極高的尺寸精度與機械強度,加工難度較高,尤其是帶內循環水路的背板,因為材質的特殊性,水路的密閉焊接非常困難,需要用到特種焊接工藝。
金屬化:靶坯與背板在綁定之前,為加強靶材和靶材與焊料的金屬潤濕性能,需要進行焊合面的預處理,使之表面鍍上一層過渡層。
綁定:大部分靶材因為材料的理學或化學性能受限,不可直接裝機鍍膜運用,需要采用金屬焊料將靶坯與背板相互焊合連接,并且表面有效粘結率需要達到大于 95%的大面積焊合,全部過程需要在高溫和高壓下進行。
2、蒸鍍材料工藝流程
其中,重點工序的詳細含義如下:
混料:指配制好的原料經過機械混合達到均勻分散的加工工藝過程,是材料加工中最重要的生產工藝之一。
原料預處理:指將混和好的原料進行常溫或高溫處理,加強材料的純度,細化顆粒的粒度,激發材料的反應活性,降低材料燒結溫度。
成型:指將材料經過機械方式達到所需規格的加工工藝工程,是材料加工中最重要的生產工藝之一。
燒結:指材料在高溫下,陶瓷生坯固體顆粒的相互鍵聯,晶粒成長,空隙(氣孔)和晶界漸趨減少,經過物質的傳遞,其總體積收縮,密度增多,最后作為擁有某種顯微結構的致密多晶燒結體的過程,是材料加工中最重要的生產工藝之一。燒結方式重點有常壓高溫燒結、真空燒結、熱壓燒結、氣氛燒結等。
鍍膜檢測:是在蒸鍍材料生產完后,采用蒸發鍍膜設備對材料的性能進行檢測,檢測制品性能指標是不是合格,是材料性能檢測中重要的檢測手段。
PVD 鍍膜材料行業上下游產業鏈
PVD 鍍膜材料產業鏈上下游關系如下:
2016 年全世界高純濺射靶材市場規模約為 113.6 億美元,其中平板表示(含觸控屏)用靶材為 38.1 億美元、半導體用靶材 11.9 億美元、太陽能電池用靶材23.4 億美元、記錄媒介靶材 33.5 億美元。到 2019 年,全世界高純濺射靶材市場規模將超過 163 億美元,年復合增長率達 13%。
PVD 鍍膜材料下游應用行業概況
1、平板表示行業
PVD 鍍膜材料在平板表示行業的應用
平板表示器重點包含液晶表示器(LCD)、等離子表示器(PDP)、有機發光二極管表示器(OLED)等,以及在 LCD 基本上發展起來的觸控(TP)表示制品。
鍍膜是現代平板表示產業的基本環節,為保準大面積膜層的均勻性,加強生產率和降低成本,幾乎所有類型的平板表示器件都會運用海量的鍍膜材料來形成各類功能薄膜,其所運用的 PVD 鍍膜材料重點為濺射靶材,平板表示器的非常多性能如分辨率、透光率等都與濺射薄膜的性能密切關聯。平板表示鍍膜用濺射靶材重點品種有:鉬靶、鋁靶、鋁合金靶、鉻靶、銅靶、銅合金靶、硅靶、鈦靶、鈮靶和氧化銦錫(ITO)靶材等。
平板表示行業鍍膜工藝示意圖如下:
平板表示行業重點在表示面板和觸控屏面板兩個制品生產環節運用 PVD 鍍膜材料。其中,平板表示面板的生產工藝中,玻璃基板要經太多次濺射鍍膜形成ITO 玻璃,而后再經過鍍膜,加工組裝用于生產 LCD 面板、PDP 面板及 OLED面板等。觸控屏的生產,則還需將 ITO 玻璃進行加工處理、經過鍍膜形成電極,再與防護屏等部件組裝加工而成。另外,為了實現平板表示制品的抗反射、消影等功能,還能夠在鍍膜環節中增多相應膜層的鍍膜。
平板表示器擁有厚度薄、重量輕、低能耗、低輻射、無閃爍、壽命長等特點,符合人們對輕巧便攜和節能環保的需求,已作為表示屏行業的主流。尤其是液晶表示器中的薄膜場效應晶體液晶表示器(TFT-LCD)因擁有畫質優、對比度高、響應速度快等特點,被廣泛應用于平板電視、手機、平板電腦、筆記本電腦等消費類電子制品,是日前主流平板表示制品。TFT-LCD 生產過程中,濺射靶材重點用于薄膜晶體管(TFT)和彩色濾光片(CF)的制備。
②觸控屏市場
觸控表示制品是平板表示行業應用行業的重要構成部分,而觸控屏是觸控表示制品的重要部件。觸控屏是一種特殊傳感器,是一個不運用鍵盤和鼠標做為輸入設備與表示設備的人機交互界面,觸控屏的顯現,統一了觸覺和視覺,使得人機交互更加直觀和方便。觸控屏最大市場需要重點來自智能手機和平板電腦,同期,車載表示和智能穿戴設備市場亦呈快速增長態勢。近年來,隨著智能手機、平板電腦、車載表示、智能穿戴及商場化信息查找系統等智能終端制品的普及推廣,全世界觸控表示制品和技術發展進步較快,產業規模持續提高。
觸控屏的結構大致可分為兩部分,分別是防護屏和觸控模組。其中,觸控模組鍍膜所用的濺射靶材重點為 ITO、硅、鉬、鋁等,采用硅靶材反應濺射形成的二氧化硅膜則重點起增多玻璃與 ITO 膜的附著力和平整性、表面鈍化和守護等功效;鍍 MoAlMo(鉬鋁鉬)膜后蝕刻重點起金屬引線搭橋的功效。防護屏重點用于守護觸控模組和表示屏免受損害,其擁有防刮耐磨、耐腐蝕、透光率高、反射率低、防油污及美觀等功能,實現這些功能需要運用區別鍍膜材料,重點為濺射靶材。
2、光學元器件行業
(1)光學元器件行業概況
光學元器件行業屬于光學產業鏈的中游,與其密切關聯的行業為光學材料生產行業及光電整機行業,其中光學材料生產行業處在光學元器件行業的上游,光電整機行業處在光學元器件行業的下游。
自從上世紀 90 年代末數字化帶動光電應用制品快速發展后,光學元器件應用行業越來越廣,從光學傳感、照明、通信技術、能量檢測、信息存儲、傳輸、處理和表示,到現代的如生命科學、汽車、航空航天等行業的生產和應用,它存在于現代人每日生活和經濟活動的大部分行業,常規的應用制品包含智能手機、車載鏡頭、安防監控設備、數碼相機、光碟機、投影機等,高端的應用制品包含航空航天監測鏡頭、生物識別設備、生命科學中 DNA 測序等科研設備、醫療檢測儀器鏡頭、半導體檢測設備以及大視場投影鏡頭(如 IMAX)、3D 打印機等儀器設備所需的光學元器件及光學鏡頭。隨著科技的進步和制造工藝的提高,智能手機、數碼相機等電子制品逐步作為居民重要的消費制品,其更新換代的加快、制品周期的縮短帶動了光學元器件行業的穩步發展。近些年來安防監控設備、車載鏡頭、航天航空行業的快速發展亦對光學元器件行業的增長起到了推動功效。
①智能手機應用市場
近年來,國內品牌手機實現大幅增長,帶動了產業鏈上游的發展。隨著智能手機的普及,攝像頭已作為手機標配,而手機廠商在推出手機新品時亦會思慮在攝像頭像素上更新升級,以迎合市場需要,攝像頭高清化作為手機廠商必爭之地。與此同期,智能手機、平板電腦配備攝像頭和雙攝像頭的比例亦在快速提高。
智能手機的更新換代帶動了光學元器件的持續發展,將來隨著 3D 手勢掌控和眼球跟蹤等功能的持續開發,智能手機廠商將在新的機型中配置更加多攝像頭以實現對以上功能的支持,對光學元器件的需要將進一步提高。
②安防監控應用市場
近年來我國出臺多項政策逐步推進安全城市概念,高清化攝像頭做為交管監控、偵查線索被廣泛應用,視頻監控市場逐步從一線城市擴大到二三線城市。
隨著公共與個人安全越來越受到注重,視頻監控市場的高速發展連續推動精細光學鏡片需要的增長,在將來幾年將繼續維持高景氣。
③車載鏡頭行業分析
隨著全世界汽車銷量的增長以及行車安全愈來愈受到人們的注重,車載攝像頭市場進入快速增長時間。車載攝像頭擁有廣泛的應用空間,根據應用行業可分為行車輔助(行車記錄儀、ADAS(高級駕駛輔助系統)與主動安全系統)、駐車輔助(全車環視)與車內人員監控,貫穿行駛到泊車的全過程,日前運用最多的是前視以及后視攝像頭,隨著 ADAS 系統滲透率加強以及人臉識別等技術運用于汽車電子行業,車內以及側視攝像頭將會得到進一步應用。
④航天航空行業
隨著人們出行、旅游、拍攝等方面需要的不斷增長,近年來軍民融合概念的逐步深化,航天航空業得到較快發展,民用與軍用無人機、雷達、空中交通工具均實現很強程度的增長,帶動了航天航空用光學元器件的發展?!吨袊圃?2025》提出,要大力推動航空航天裝備等重點行業突破發展。將來隨著無人機等廣泛應用于影視宣傳航拍航攝、農林業植保、電力巡檢、國家應急救援、物流物資運輸、交通監察、環境監測等,航天航空用光學元器件有望迎來下一波快速發展。
(2)鍍膜材料在光學元器件行業的應用
因為現代精細光學元件向功能集成化和高精度方向發展,光學元器件的分光光譜特性等需依靠光學鍍膜實現,光學鍍膜技術已作為光學元器件行業的關鍵技術之一,運用的 PVD 鍍膜材料包含濺射靶材和蒸鍍材料。
光學元器件鍍膜指的是在光學元器件上或獨立的基板材料上鍍上一層或多層,乃至數百層的介電質膜、金屬膜、介電質膜與金屬膜構成的膜系,來改變光波傳導的特性,包含光的透射、反射、吸收、散射、偏振及相位改變。精細光學鍍膜的偏振分光、減反射、光譜波長準確定位(一般在納米級)等特性是日前其他技術難以替代的,因此光學鍍膜技術是光學元器件加工的關鍵技術,其擁有較高的技術門檻,日前有效、高品質、低成本的批量化生產技術仍然僅有少許光學加工企業把握。
近年來,濺射鍍膜等鍍膜技術起始應用于光學鍍膜,提高效率和良品率、降低成本效果顯著,作為實現大批量生產精細光學元器件的重要技術。
將來受益于全世界及中國光學元器件行業與技術的發展,將對 PVD 鍍膜材料的需要有著直接的拉動功效。
3、其他下游應用行業
(1)半導體行業
半導體產業重點由集成電路、半導體分立器件、光電器件和傳感器等制品形成,其中集成電路是半導體產業最大的構成部分,也是濺射靶材重要應用行業。信息技術的飛速發展,需求集成電路的集成度越來越高,電路中單元器件尺寸持續縮小,元件尺寸由毫米級到微米級,再到納米級。每一個單元器件內部由襯底、絕緣層、介質層、導體層及守護層等構成,其中,介質層、導體層乃至守護層都要用到濺射鍍膜工藝,濺射靶材是制備集成電路的核心材料之一。
集成電路中所運用的薄膜制品包含電極互連線膜、阻擋層薄膜、接觸薄膜、光刻薄膜、電容器電極膜、電阻薄膜等,運用的濺射靶材重點包含鋁靶、鈦靶、銅靶、鉭靶、鎢鈦靶等。
(2)太陽能電池行業
太陽能光伏行業中,PVD 鍍膜材料重點應用于太陽能電池。按太陽能電池的結構劃分,可分為結晶硅和薄膜太陽能電池二大族群。日前,PVD 鍍膜工藝重點在薄膜太陽能電池中運用,重點鍍膜材料為濺射靶材。其中,較為常用的濺射靶材包含鋁靶、銅靶、鉬靶、鉻靶以及 ITO 靶、AZO 靶( Aluminum Zinc Oxide,氧化鋁鋅)等,純度需求通常在 99.99%以上,其中,鋁靶、銅靶用于導電層薄膜,鉬靶、鉻靶用于阻擋層薄膜,ITO 靶、AZO 靶用于透明導電層薄膜。
結晶硅技術長時間在太陽能電池產業中占據主流地位,因為其成本較高,業內始終經過提高電池轉換效率、降低硅片切割厚度等技術來降低成本;與此同期,薄膜太陽能電池因其生產成本低、弱光性好(即在陰天發電能力強)、容易集成等優良,逐步受到行業關注并增長快速,將來薄膜太陽能電池市場占有率將逐步加強。
(3)磁記錄媒介行業
光磁記錄媒介重點包含光記錄媒介與磁記錄媒介兩種,采用濺射鍍膜工藝進行鍍膜。其中,光記錄媒介按照盤片的類別和功能區別,鍍膜的需求亦區別,重復讀寫型盤片工藝最繁雜,需要鍍三層膜,分別為反射層、介電層和記錄層;其余盤片則只需鍍反射層或半反射層。光記錄媒介需求濺射靶材擁有良好的薄膜特性、濺鍍效率、清凈度、晶像均勻性和回收系統等特性。磁記錄媒介需求濺射靶材擁有高純度、低氣體含量、細晶微結構、均勻的金相、高磁穿透和運用率、優異的電性與機械特性等。
(4)節能玻璃行業
日前,PVD 鍍膜材料在節能玻璃行業重點應用于建筑節能玻璃及汽車鍍膜玻璃這兩個行業中,鍍膜材料重點為濺射靶材。
濺射靶材在建筑節能行業重點用于低輻射鍍膜玻璃(Low-E 玻璃),Low-E玻璃是在玻璃表面鍍上多層金屬或其他化合物構成的膜系制品,該制品對可見光有較高的透射率,對紅外線(尤其是中遠紅外)有較高的反射率,擁有良好的隔熱性能,能達到掌控陽光、節約能源、熱量掌控調節及改善環境的功效,是日前全世界重點的建筑節能玻璃。
在汽車鍍膜玻璃中,濺射靶材日前重點用于汽車前風窗玻璃上,汽車鍍膜玻璃是采用濺射鍍膜技術,在玻璃內表層鍍上多層納米級的金屬膜,使太陽光的紅外線有效的被反射,阻隔熱能進入車身體,降低空調負荷,同期維持良好的透光性,保持視野的清晰,較好的處理了貼膜玻璃存在的缺陷。在歐美等發達國家,鍍膜玻璃已做為中高檔轎車的標準配置,隨著我國人民生活水平的加強,汽車鍍膜玻璃已得到越來越多汽車制造商和消費者的喜愛。
行業內重點企業
1、重點跨境企業
(1)世泰科
世泰科集團(H.C.Starck)1920 年于德國柏林成立,是一家國際跨境集團,總部位置于德國慕尼黑,世泰科致力于客戶化的高性能金屬與陶瓷粉末以及金屬制品的開發與生產,其鉭粉、鎢粉、鉭質濺射靶材以及鎳鈮制品全世界市場占有率排名前列,是擁有全世界領先技術的金屬循環利用商。
世泰科特種材料(太倉)有限機構是世泰科在中國設立的從事新材料的子機構,成立于 2006 年 5 月 8 日,注冊資本 1,392 萬美元,經營范圍:生產有色金屬復合材料、新型合金材料、陶瓷材料、表面處理材料和電子助劑,營銷機構自產制品并供給關聯技術咨詢和售后服務;從事本機構生產的同類制品的批發、進出口及傭金代理業務(拍賣除外)。
(2)賀利氏
賀利氏集團(Heraeus)成立于 1851 年,總部位置于德國哈瑙市,是國際著名的集貴金屬化工制品開發、生產及營銷服務的高科技跨境集團機構,重點從事貴金屬材料與技術、齒科材料、石英玻璃、工業傳感器和特種光源等高新技術行業,制品廣泛服務于半導體行業,其中高純石英和濺射靶材、蒸發材料應用于芯片制造、導電膠和鍵合絲應用于集成電路、分立器件和光電器件的封裝。
上海賀利氏工業技術材料有限機構是賀利氏在中國設立的從事新材料的子機構,成立于 1994 年 9 月 19 日,注冊資本 810 萬美元,經營范圍:回收利用、加工、生產銥粒,催化網,鉑族(鉑、銠、鈀、釕、銥、鋨)化合物,電子漿料,陶瓷顏料,鉑金漏板,硬質合金軸承珠和微型刀具,鉑銠熱電偶絲和配件,實驗室用鉑金器皿,模壓塑料/金屬組體,用鈦、鈮、鋯和鉭制成的電極和耐腐管子管材,真空靶材,母合金顆粒,電路、零部件材料及鈀、銠、銥、釕、鋨、硅樹脂、鍺、鉻、銦和錫材料,金屬和陶瓷類義齒材料,營銷自產制品。
(3)優美科
優美科集團(Umicore)是一家全世界材料科技集團,總部位置于比利時。優美科持有四大業務集團:催化、能源材料、高性能材料和回收。每一個業務集團又劃分為以市場為導向的區別業務單位,這些業務單位供給走在技術發展前沿并且是平常生活所必需的材料和處理方法。優美科在全世界各大洲開展運營,客戶群遍及全世界。優美科2014-2016年度的營銷額分別是88.28億歐元、104.42 億歐元、110.86億歐元。
優美科先導薄膜技術有限機構是優美科在中國設立的從事濺射靶材的子機構,于 2014 年 9 月 11 日在廣東省清遠市成立,注冊資本為 14,000 萬元,經營范圍:在中國行業內研發、生產、綁定、營銷和營銷平板及旋轉氧化銦錫(“ITO”)濺射靶材(“ITO”靶材);為生產 ITO 靶材或蒸鍍級 ITO,在中國行業內研發、生產、營銷和營銷以下中間品:氧化銦、氫氧化銦、ITO 粉末和 ITO 丸;在中國行業內回收 ITO 廢靶、ITO 生產廢料和運用 ITO 靶材產生的副制品;為金屬套期保值和庫存管理的目的營銷銦。
北京優美科巨玻薄膜制品有限機構是優美科在中國設立的從事光學鍍膜材料生產的子機構,成立于 1991 年 11 月 21 日,注冊資本 54 萬元,經營范圍:生產光學鍍膜材料和制品及其它薄膜鍍膜材料和制品;營銷自產制品等。
(4)普萊克斯
普萊克斯機構(Praxair)總部位置于美國,是世界最大的氣體供應商之一,該機構最初創建于 1907 年,重點制品包含大氣氣體制品、生產氣體制品以及表面技術制品。普萊克斯機構重點服務于航空航天、化工、醫療保健、金屬生產、石油天然氣、能源、電子等行業,其中其電子行業的重點制品包含電子設備、大氣氣體傳送系統、濺射靶材等,其濺射靶材重點應用于電子及半導體行業。
2014-2016 年度,普萊克斯營銷額分別為 122.73 億美元、107.76 億美元、105.34億美元,其中濺射靶材所屬的表面技術制品營銷額分別為 6.79 億美元、6.09 億美元、5.96 億美元。
(5)霍尼韋爾
霍尼韋爾國際機構(Honeywell International Inc.)成立于 1885 年,總部位置于美國,持有航空航天集團、自動化掌控系統集團以及特殊材料和技術集團三大業務分部。其中特殊材料和技術集團下屬特性材料業務分部,重點制品之一電子原材料包含熱界面材料、電子化學品、電子聚合物、貴金屬熱電偶、靶材、線圈組和金屬材料等。霍尼韋爾的重點靶材包含鈦鋁靶、鈦靶、鋁靶、鉭靶、銅靶等。
2014-2016 年度霍尼韋爾營銷額分別為 403.06 億美元,385.81 億美元、393.02 億美元,其中靶材所屬的新材料營銷額分別為 39.04 億美元、35.10 億美元、33.27億美元。
(6)住友化學
住友化學株式會社(Sumitomo Chemical Company, Limited)成立于 1913 年,總部位置于日本,重點服務于石油化學、能源-功能材料、情報電子化學、健康-農業關聯事業和醫藥五大行業。其中情報電子化學向 ICT 關聯產業供給液晶表示器中運用的光學薄膜和彩色光阻劑,半導體制造過程中運用的光刻膠和高純度藥物,電子零部件和電動汽車所運用的超級工程塑料,以及鋰離子二次電池用構件等各類制品。2014-2016 財年(上年 4 月 1 日至當年 3 月 31 日),住友化學營銷額分別為 2.24 萬億日元,2.38 萬億日元、2.10 萬億元,其中濺射靶材所屬的情報電子化學行業營銷額分別為 3,623 億日元、4,051 億日元、4,091 億日元。住友化學在國內設立的子機構中從事新材料關聯業務的有住化電子材料科技(無錫)有限機構、住化電子材料科技(上海)有限機構、住化華北電子材料科技(北京)有限機構三家機構。
住化電子材料科技(無錫)有限機構成立于 2004 年 7 月 26 日,注冊資本16,222.22 萬美元,經營范圍:研發、生產半導體、元器件專用材料、電子用高科技化學品、工程塑料、塑料板;并供給售后服務、技術服務;自有廠房租賃;從事以上制品的批發、零售、傭金代理及進出口業務,設備租賃。
住化電子材料科技(上海)有限機構成立于 2001 年 9 月 14 日,注冊資本 777.78 萬美元,經營范圍:區內光學用多功能薄膜的生產加工及光學用多功能薄膜加工設備、器械(斜角剪切機、壓力貼合機、半裁機、萬能剪切機、重繞機)的制造,金屬鎵的精制、加工;應用于液晶面板及半導體前制程的濺射靶材與靶材襯底的貼合加工,以及其他相關液晶表示器用零部件的制造;營銷自產制品等。
住化華北電子材料科技(北京)有限機構成立于 2009 年 11 月 16 日,注冊資本 4,366.67 萬美元。經營范圍:生產 TFT-LCD 平板表示屏材料;TFT-LCD 平板表示屏材料的研發;技術咨詢、技術服務;營銷自產制品;TFT-LCD 平板表示屏材料、電子材料的批發、傭金代理(拍賣除外)、進出口業務。
(7)東曹
東曹株式會社(Tosoh Corporation)成立于 1935 年,總部位置于日本,其功能制品分部由有機化學制品、高機能材料制品、生命科學三部分構成,其中高機能材料制品重點包含電池材料、石英玻璃、分子篩、濺射靶材等。其濺射靶材經過在美國、日本、韓國和中國的生產基地生產,重點用于半導體、太陽能發電、平板表示器、磁記錄媒介等行業。2014-2016 財年(上年 4 月 1 日至當年 3 月 31日)東曹營銷額分別為 7,722.72 億日元、8,096.84 億日元、7,537.36 億日元。
東曹達(上海)電子材料有限機構是東曹株式會社在中國設立的觸及濺射靶材業務的子機構,成立于 2011 年 7 月 6 日,注冊資本 100 萬美元,經營范圍:開發、生產、加工機電、電子、半導體、光能設備、關聯材料制品(濺射靶材、石英)及以上關聯制品零部件,營銷機構自產制品,并供給倉儲;同類商品(特定商品除外)的批發、進出口、傭金代理(拍賣除外)及關聯制品售后技術、咨詢等配套服務;電子材料科技行業內的技術研發、技術咨詢、技術服務及技術轉讓業務。
(8)JX 金屬
JX 金屬株式會社(JX Nippon Mining & Metals Corporation)成立于 1992 年,為 JX 控股子機構。JX 控股總部位置于日本,重點有能源業務、石油天然氣探測和生產業務、金屬業務三大業務,其中金屬業務為 JX 金屬運營,JX 金屬以銅為中心,致力開展從上游的資源研發、中游的金屬冶煉至下游的電子材料加工、環保資源再生業務,重點制品包含銅箔、復合半導體、金屬粉末、濺射靶材等,其中濺射靶材重點用于大規模集成電路、平板表示、相變光盤等。2014-2016 財年(上年 4 月 1 日至當年 3 月 31 日)JX 控股與金屬業務關聯的營銷額分別為 10,391億日元、11,560 億日元和 10,497 億日元。
(9)愛發科
日本愛發科真空技術株式會社(ULVAC,Inc.)成立于 1952 年,總部位置于日本,設有真空設備分部和真空應用分部,重點制品分為真空設備、真空組件和原材料三大類,其中原材料包含高性能材料和濺射靶材,其濺射靶材重點應用于平板顯示、半導體、太陽能電池等行業,另外愛發科還能夠生產 ITO 靶材。2014-2016財年(上年 7 月 1 日至當年 6 月 30 日),愛發科的營銷額分別 1,738.78 億日元、1,791.74 億日元、1,924.37 億日元,其中 2014、2015 財年濺射靶材所屬的真空應用分部的營銷額分別為 360.68 億日元、315.33 億日元、320.00 億日元。
愛發科真空技術(蘇州)有限機構是愛發科中國設立的觸及濺射靶材業務的子機構,成立于 2003 年 7 月 8 日,注冊資本為 3,450 萬美元,經營范圍重點是:液晶、半導體生產用安裝,真空爐,真空關聯安裝、零部件的科研研發、生產、加工,營銷其制品并供給售后服務。自有多余廠房出租(出租對象僅限于與本機構生產經營直接相關的或集團內部企業);本機構生產制品的同類商品及原材料的批發、進出口、傭金代理(拍賣除外)及關聯業務。
(10)三井礦業
三井礦業冶煉有限機構(Mitsui Mining & Smelting Co.,Ltd.)成立于 1950 年,主營業務包含工程材料、電子材料制造和營銷,非鐵金屬加工、資源研發、貴金屬回收、原材料關聯事業,汽車配件制造和營銷等。2014-2016 年度的營銷額分別為 4,410.46 億日元、4,732.74 億日元、4,506.53 億日元。其中 PVD 鍍膜材料所屬分部 2014、2015 年度的營銷額分別為 1,366 億日元、1,532 億日元、1,440 億日元。
(11)攀時
奧地利攀時集團(Plansee)成立于 1921 年,是專注于生產、加工與營銷難熔金屬鉬與鎢的供應商,攀時集團旗下包含三個業務群與一個控股機構:攀時高性能材料制造難熔金屬部件、森拉天時制造硬質合金刀具、GTP 為集團供應鎢精礦、Molymet 為集團供應鉬精礦。
攀時運用鋁、鈦、鋯、鉻等金屬與陶瓷材料生產濺射靶材與電弧陰極。攀時濺射靶材與電弧陰極的性能尤其之處:優異的材料純度;極高的材料密度;極其精細的晶粒以及微觀結構。2015 年度、2016 年度,攀時的營銷額分別為 11.82億歐元、21.68 億歐元。
(12)佳能
佳能機構(Canon Inc.)1937 年創立,總部位置于日本東京,與美洲、歐洲、亞洲和大洋洲的各區域總部緊密聯系,構筑了全世界化與本土化有機結合的經營體制。日前,佳能事業以光學技術為核心,涵蓋了影像系統制品、辦公制品以及產業設備等廣泛行業。其中,產業設備及其他事業行業重點包含:數碼印刷系統、生產型照片輸出系統、業務用高速連續紙打印機、彩色標簽/卡片打印機、眼科設備、安防監控攝像機、工業相機、半導體揭發設備、FPD(平板表示器)揭發設備、液晶表示屏制造設備、混合現實系統、3D 設備視覺系統、手持終端、元件、固晶體、真空鍍膜設備等。2014-2016 年度佳能營銷額分別是 37,272.52 億日元、38,002.71 億日元、34,014.87 億日元。
(13)默克
德國默克集團(Merck)成立于 1668 年,默克包含醫藥健康、生命科學、高性能材料等事業部,其中高性能材料事業部包含多種特殊化學制品,如液晶表示屏、用于涂料和打扮品的效果顏料,或是電子行業的高新技術材料。2014-2016年度,默克營銷額分別為 422.37 億美元、394.98 億美元和 398.07 億美元。
2、國內重點 PVD 鍍膜材料廠商
日前中國涌現了一批 PVD 鍍膜材料行業的參與者,其中以有研億金、江豐電子和阿石創擁有表率性;同期,隆華節能經過收購其他 PVD 鍍膜材料廠商的股權介入 PVD 鍍膜材料行業。有研億金、江豐電子與隆華節能簡介如下:
(1)有研億金
有研億金新材料有限機構為有研新材料股份有限機構(600206.SH)之全資子機構,成立于 2000 年 10 月,總部位置于北京,注冊資本 20,000 萬元,有研億
金重點開發、生產、營銷微電子光電子用薄膜新材料、生物醫用新材料、貴金屬材料及制品,并開展稀有及貴金屬材料信息咨詢、技術服務和套期保值等業務;重點制品包含高純金屬靶材、蒸鍍材料、口腔正畸器具、醫療用介入支架和貴金屬合金、化合物等,其靶材制品重點包含鋁及其合金靶材、鈦靶、銅靶、鉭靶等。
(2)江豐電子
寧波江豐電子材料股份有限機構成立于 2005 年 4 月,注冊資本 21,876.00萬元。江豐電子主營業務為高純濺射靶材的開發、生產和營銷,重點制品為各樣
高純濺射靶材,包含鋁靶、鈦靶、鉭靶、鎢鈦靶等,重點用于制備電子薄膜材料。
日前,江豐電子制品重點應用于半導體、太陽能電池及平板表示器等行業。
(3)隆華節能
洛陽隆華傳熱節能股份有限機構(300263,SZ)成立于 1995 年 7 月 5 日,于 2011 年 9 月 16 日在創業板上市,主營業務為熱傳節能制品、環保水處理制品及服務。隆華節能分別于 2015 年和 2016 年經過收購洛陽高新四豐電子材料有限機構和廣西晶聯光電材料有限責任機構介入 PVD 鍍膜材料行業。四豐電子和晶聯光電基本狀況如下(資料來源:隆華節能定時報告及關聯公告、國家企業信用信息公示系統):
四豐電子成立于 2001 年 6 月,日前注冊資本 7,000.00 萬元,重點從事高純金屬及合金材料業務,制品以鉬靶材為主。2015 年 1 月,隆華節能完成對四豐電子 100%的收購,并于 2016 年 2 月起將其納入合并報表范圍。
晶聯光電成立于 2007 年 9 月,日前注冊資本 8,453.5747 萬元,重點從事氧化銦錫(ITO)靶材的開發、生產和營銷;2016 年 8 月 24 日,隆華節能發布《關于對外投資的公告》,經過股權轉讓及增資方式持有晶聯光電 70%股權。
國內競爭與前景
靶材隸屬于成膜的材料類,成膜材料又分為:蒸發材料/濺射靶材等等形式,靶材的應用:
1 面板行業:便是一般所說的TFT-LCD還有OLED制程,國內的重點生廠商有BOE(京東方)/天馬/華星等等;用到的靶材有:鉬靶/鋁靶/ITO靶/硅靶/硅鋁等等 靶材生產廠家:攀時(奧地利),GFE,賀利士,梭萊(美國)等等,國內的的廠家介入較早的是隆華節能旗下的四豐電子;阿石創……
總結:這個行業呢此刻好的制程基本都是進口,由于進口的相針對國內的質量比較穩定,價格貴一點平攤下來亦顯不出多貴來了。
2 半導體行業:半導體行業除了硅片的行業不消靶材以外,幾乎每一個制程都要用到濺射鍍膜機或說是每一個制程都要用來鍍膜或是水鍍或是PVD;會運用到的靶材有:金靶/銀靶/鉑金靶材/等等 運用靶材的機構:長電科技,中國電子,紫光,中芯國際,華微電子,順絡電子,東晶電子,泰晶科技,富士通/士蘭微電以及各式各樣的科研所等等等等,總之是太多太多 靶材機構:寧波江豐/有研新材/招金勵福(上市排隊中)/光陽化學(臺灣機構,老板已然被臺灣檢方帶走了,炒期貨賠了N億,阿石創
3 太陽能行業:太陽能行業僅限薄膜太陽能才可用到PVD鍍膜,行業內最大的便是漢能了;然則漢能和他的全資子機構之間。。。。呵呵;所用的靶材:此刻已然發展到用銅銦鎵硒的技術了;靶材生產廠商:贛州研創(臺灣機構)/深圳歐萊等等等等 4 Low-e樓宇玻璃鍍膜行業:前幾年搞大躍進,這個行業是產能過剩行業,利潤最低的機構,比很強的機構有信義玻璃/南玻A/耀皮玻璃/臺玻;所用靶材:銀靶/鎳鉻靶材/AZO(陶瓷靶)/硅鋁等等 靶材廠:梭萊(美國)/安泰科技/招金勵福(再排隊)/阿石創 等等。
4、還有便是刀具鍍膜/外觀鍍膜/柔性鍍膜等等等等
其實咱們所能用的東西中非常多的都是要用來鍍膜的。
附:光學鍍膜技術與應用:薄膜及其特性講解